2025 Autor: Howard Calhoun | [email protected]. Zuletzt bearbeitet: 2025-06-01 07:13
Granuläre Hochofenschlacke ist ein Abfall der metallurgischen Produktion. Genauer gesagt handelt es sich dabei um den Rohstoff, der nach dem Schmelzen von Roheisen in Hochöfen übrig bleibt.
Was ist Schlacke und wo kommt sie her?
Um Rohstoffe wie Roheisen herzustellen, müssen bestimmte Rohstoffe in den Hochofen geladen werden. Solche Materialien waren Eisenerz, Flussstein, Koks. Am Ausgang des Ofens werden nur zwei Substanzen erh alten - das ist Roheisen und Schlacke. Die Zusammensetzung der Hochofenschlacke umfasst Stoffe wie Quarz, Aluminiumoxide (Aufbereitung aus Eisenerz), Calcium- und Magnesiumoxide (Abfälle aus Flusssteinen). Die geschmolzene Schlacke, die am Ausgang des Hochofenblocks anfällt, kann eine Temperatur von 1500 Grad Celsius und in einigen Fällen sogar noch mehr haben. Natürlich ist eine Kühlung des Materials erforderlich. Derzeit verwenden die Anlagen nur 4 Hauptarten der Hochofenschlackenverarbeitung.
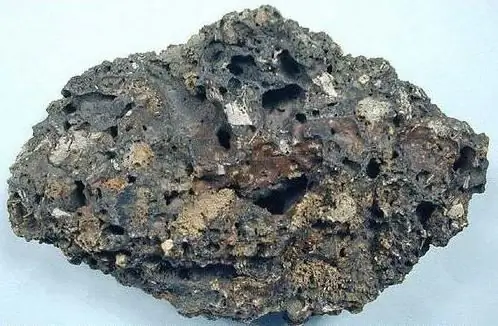
- Die erste Methode besteht darin, das Rohmaterial mit normalem k altem Wasser zu kühlen. Dieser Vorgang wird auch Schlackenquellung genannt.
- Die zweite Methode verwendet KühlungSubstanzen mit Hilfe von Luft.
- Der dritte Weg ist das Zermalmen.
- Vierte - Schleifen.
Hauptmaterialkomponenten und Verarbeitungsergebnisse
Hier ist zu beachten, dass die Wahl des Verfahrens zur Verarbeitung von Hochofenschlacke darüber entscheidet, welche Art von Stoff am Ende erh alten wird und welche Eigenschaften er haben wird. Jede Methode verleiht dem Rohmaterial einzigartige Qualitäten. Eine weitere wichtige Beobachtung ist, dass die Hauptoxide, die Bestandteil der Schlacke sind - Oxide von Magnesium, Calcium und Aluminium - in der Natur nicht in freier Form vorkommen. Mit anderen Worten, sie existieren nicht und können nur durch die Verarbeitung von Schlacke und Eisenerz im Hochofen gewonnen werden. Die Zusammensetzung des Stoffes umfasst neben den Hauptoxiden Mangan, Eisen- und Schwefelverbindungen, Quarz.
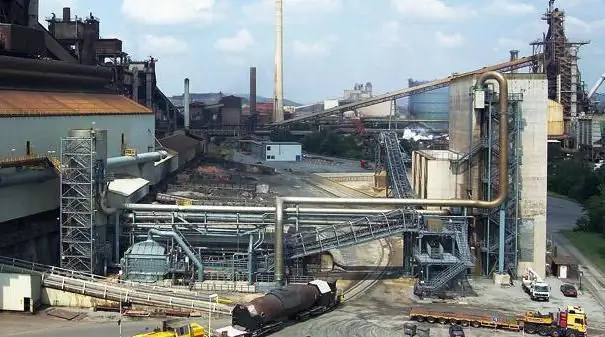
Wenn Sie beispielsweise das verbrauchte Material mit Luft kühlen, wird die Zusammensetzung der Hochofenschlacke ungefähr wie folgt sein: Silikate und Alumosilikatmaterialien wie Wolastonit, Melilit und Merwinit.
Wie läuft der Granulationsprozess ab?
Der Prozess der Granulierung einer Substanz wird durch die Methode der schnellen Abkühlung der geschmolzenen Rohstoffe durchgeführt. Wichtig ist hier anzumerken, dass in manchen Fällen ein mechanischer Zerkleinerungsprozess hinzugefügt werden kann, entweder noch flüssige Schlacke oder bereits halberstarrte Schlacke. Der Hauptzweck dieses Vorgangs besteht darin, große Materialstücke zu kleineren Körnern zu verarbeiten, die in Zukunft bequemer verarbeitet werden können, sowie die Qualität wie die hydraulische Aktivität zu verbessern. Dasein sehr wichtiger Vorgang, da diese Eigenschaft die wichtigste ist, da Schlacke als Bestandteil von Schlackenzementen verwendet werden kann und auch als Zusatz zu Portlandzement wirken kann.
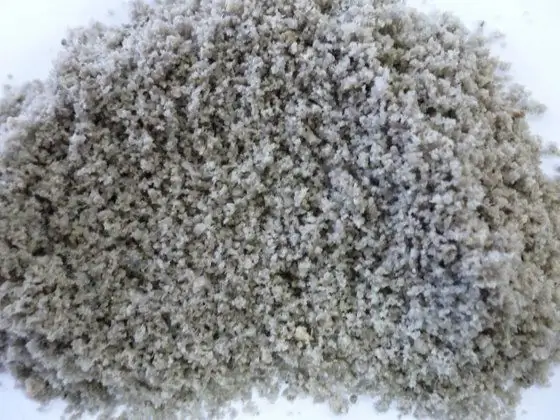
Sie müssen verstehen, dass es keine spezielle Produktion von Hochofenschlacke als solche gibt. Es wird nur durch die Verarbeitung von Erz und anderen Stoffen im Hochofen gewonnen.
Granulierungsmethoden
Sie müssen wissen, dass es für die Granulierung von Produktionsabfällen, dh Schlacke, mehrere Methoden sowie Geräte gibt, die diesen Vorgang ausführen. Je nachdem, welcher Feuchtigkeitsgeh alt der Schlacke am Ende erh alten wird, werden die Anlagen in Typen eingeteilt. Es gibt Anlagen zur Nass- und Halbtrockengranulierung.

Wird das Verfahren der Nassgranulierung durchgeführt, so wird die in die Schlackekübel geladene Schlacke in heißer Form in mit Wasser gefüllte Stahlbetonbecken geleitet. Danach geht es von den Pfannen durch spezielle Rinnen in diese Becken über. Ein kleiner Vorteil der Methode ist, dass die Becken in mehrere Abschnitte unterteilt sind. Dadurch kann der Kühlprozess nahezu kontinuierlich durchgeführt werden. Wenn die glühende Substanz in einen Abschnitt übergeht, kann gleichzeitig die bereits abgekühlte Hochofenschlacke aus dem anderen Abschnitt entladen werden. Für den Transport der Rohstoffe verfügen die Fabriken über Zweischalenkräne, die sie direkt an offene Eisenbahnwaggons liefern. Danach wird die Schlacke entweder zum Lager oder direkt zum Verbraucher geliefert.
Inh altFeuchtigkeit
Hier ist anzumerken, dass der Feuchtigkeitsgeh alt des Materials vom Gesamtgewicht der Hochofenschlacke abhängt, die den Granulationsprozess durchläuft. Mit anderen Worten, je poröser die Struktur der Körner ist, desto mehr Feuchtigkeit verbleibt in ihnen. Die Bildung von Poren in der erstarrten körnigen Schlacke erfolgt durch Einwirkung von Gasen. Diese flüchtigen Substanzen sind im geschmolzenen Rohmaterial enth alten und beginnen zu verdampfen, wenn die Temperatur der Schlacke sinkt, dh wenn sie abgekühlt wird. Hierbei ist jedoch zu beachten, dass die Abkühlung und Verfestigung des Materials so schnell erfolgt, dass das Gas keine Zeit hat, aus der Schlacke zu verdampfen. Es verbleibt in Form kleiner Bläschen im Inneren, die die poröse Struktur der Körner bilden. Die Porosität und damit der Feuchtigkeitsgeh alt der Schlacke hängen auch direkt von den Bedingungen ab, die direkt beim Kühlprozess der Schlacke verwendet werden. Das heißt, nicht nur das Endergebnis, sondern auch die Struktur selbst hängt von der Wahl der Methode ab.
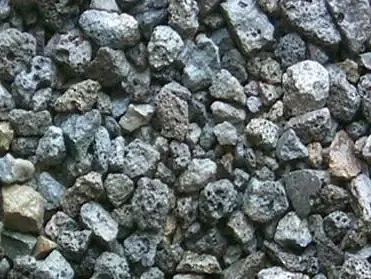
Halbtrockenmethode
Halbtrockene Schlacke wird durch die Methode der mechanischen Zerkleinerung sowie durch das Werfen der vorgekühlten, aber noch nicht erstarrten Schlacke in die Luft gewonnen. Dadurch fällt die Struktur des Materials viel dichter aus, was das physikalische Gewicht deutlich um etwa das Eineinhalbfache erhöht, verglichen mit dem Gewicht, das die Schlacke hätte, wenn sie durch die Nassgranulierung geleitet würde, mit der gleichen Anfangsmenge von Substanz. Wenn wir von einem Merkmal wie Feuchtigkeit sprechen, liegt dieser Wert für feuchte Rohstoffe durchaus im Bereich von 15 bis 35%selten 10%. Während die Trockengranulierung von einer Schlackenfeuchtigkeit im Bereich von 5 bis 10% begleitet wird. Wenn wir das Volumengewicht vergleichen, liegt es bei einer Nassverarbeitung im Bereich von 400 bis 1000 kg / m und bei einer Trockenmethode im Bereich von 600 bis 1300 kg / m. Hier ist anzumerken, dass mit steigender Hochofenschmelztemperatur das Endgewicht der Hochofenschlacke abnimmt.
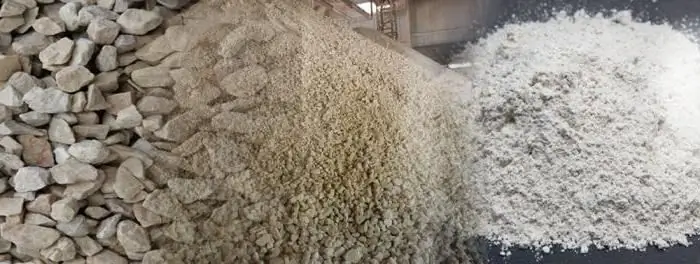
Es ist wichtig hinzuzufügen, dass die meisten Fabriken die Nassgranulierung verwenden, obwohl das Verfahren mehrere Nachteile hat:
- Hoher Kraftstoffverbrauch zum Trocknen des Materials, bevor es bricht.
- Die Produktivität von Schlackentrocknungsanlagen ist gering.
- Einfrieren nasser Schlacke in Waggons, Lagern und anderen Lagerbereichen im Winter.
Hochofenschlacke GOST 3476-74
Diese Norm beschreibt alle technischen Anforderungen, Prüfverfahren und Abnahmeregeln sowie Verfahren zur Lagerung und zum Transport von Hochofenschlacke. Einer der Punkte des Staatsdokuments betrifft den Feuchtigkeitsgeh alt von Rohstoffen. Es wird gesagt, dass der Prozentsatz der Feuchtigkeit dem entsprechen muss, was zwischen dem Kunden und dem Lieferanten vereinbart wurde. Mit anderen Worten, man kann sagen, dass der Kunde die Methode der Materialgranulierung wählt.
Empfohlen:
Kunstharze: Herstellung, Zusammensetzung, Struktur und Umfang
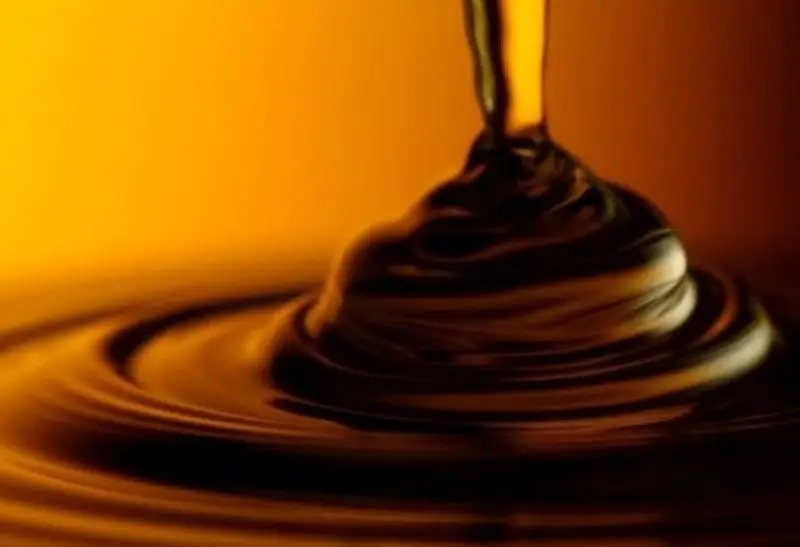
Chemikalien werden in verschiedenen Phasen des Produktionsprozesses und im täglichen Leben eingesetzt. Eine dieser Sorten sind Kunstharze. Diese Stoffe unterscheiden sich in Zusammensetzung und Umfang. Der Einsatzzweck von Kunstharzen kann sehr vielfältig sein. Abhängig von der Herstellungsmethode und Zusammensetzung werden ihre Haupteigenschaften bestimmt. Harze künstlichen Ursprungs werden weiter diskutiert
Stahl: Zusammensetzung, Eigenschaften, Arten und Anwendungen. Zusammensetzung aus Edelstahl
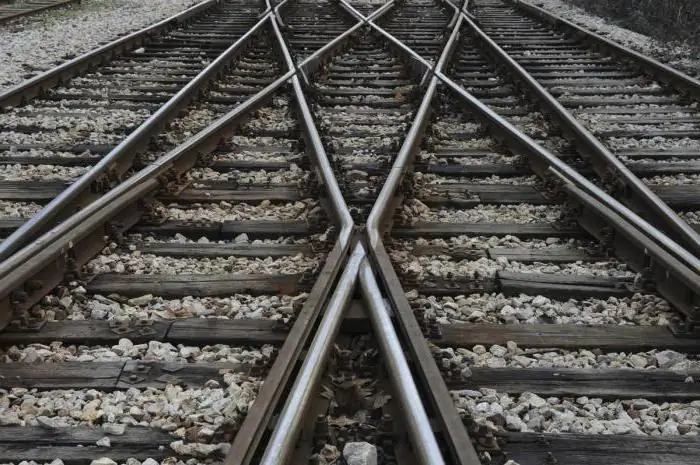
Stahl wird heute in den allermeisten Industrien verwendet. Nicht jeder weiß jedoch, dass sich die Zusammensetzung von Stahl, seine Eigenschaften, Arten und Anwendungen stark vom Herstellungsprozess dieses Produkts unterscheiden
Verzinntes Kupfer: Konzept, Zusammensetzung, Herstellung, Eigenschaften und Anwendung
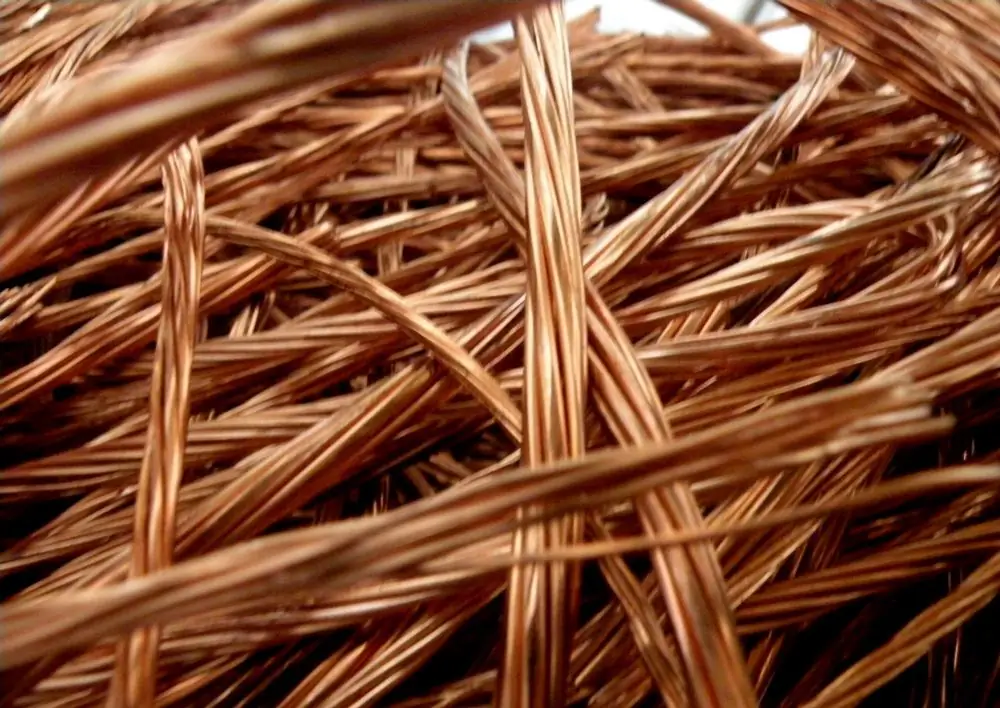
Verzinnen bedeutet, Metallprodukte mit einer dünnen Zinnschicht zu überziehen, die wiederum den Prozess der Oxidation von Metalloberflächen verhindert. Wenn wir jedoch die Wartung des Lötkolbens berücksichtigen, ist der Prozess etwas anders
Rübenschnitzel granuliert: Herstellung, Anwendung, Zusammensetzung
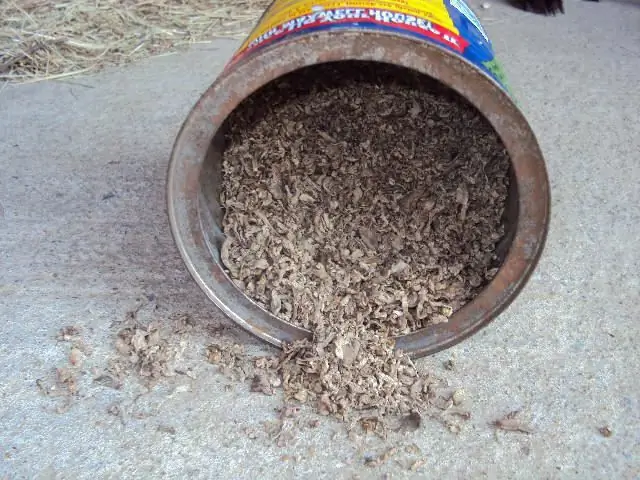
Rübenschnitzel sind ein wertvolles Futtermittel mit einem hohen Anteil an Kohlenhydraten. Es wird hauptsächlich in Granulatform verkauft
Titancarbid: Herstellung, Zusammensetzung, Zweck, Eigenschaften und Anwendungen
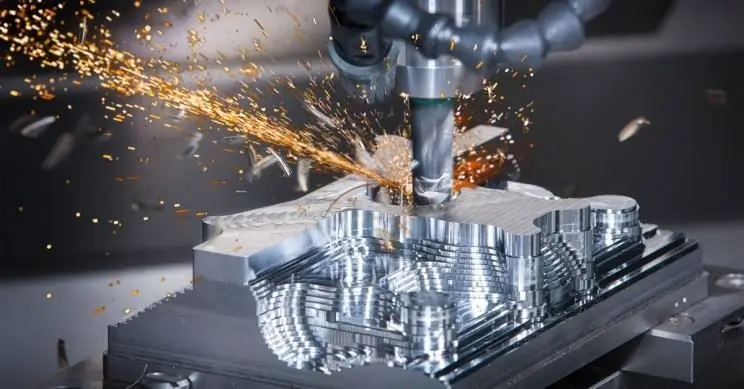
Titancarbid: die Geschichte der Entdeckung dieser Verbindung, chemische und physikalische und mechanische Eigenschaften. Beschreibung, wie Sie es erh alten. Teilebeschichtung, Karbidstahlherstellung und andere Titankarbidanwendungen