2025 Autor: Howard Calhoun | [email protected]. Zuletzt bearbeitet: 2025-06-01 07:13
Der Chef eines jeden Unternehmens, egal in welchem Tätigkeitsbereich, träumt davon, dass die Gewinne wachsen und die Produktionskosten unverändert bleiben. Das „5S“-System in der Produktion (in der englischen Version 5S), das nur auf der rationalen Nutzung interner Reserven basiert, hilft, dieses Ergebnis zu erreichen.
Dieses System wurde nicht von Grund auf neu erstellt. Etwas Ähnliches schlug Ende des 19. Jahrhunderts der Amerikaner Frederick Taylor vor. In Russland tat dies der Wissenschaftler, Revolutionär, Philosoph und Ideologe A. A. Bogdanov, der 1911 ein Buch über die Prinzipien des wissenschaftlichen Managements veröffentlichte. Auf der Grundlage der darin enth altenen Bestimmungen führte die UdSSR das NOT ein, dh die wissenschaftliche Organisation der Arbeit. Aber das perfekteste war das 5C-System, das vom japanischen Ingenieur Taiichi Ohno vorgeschlagen und von ihm im Toyota Motor-Werk in Produktion gebracht wurde. Was ist das und warum ist das japanische System so beliebt geworden?
Fakt ist, dass es auf einem einfachen Prinzip basiert, das keine Kosten verursacht. Es besteht darindas nächste - jeder Mitarbeiter, von der Reinigungskraft bis zum Direktor, sollte seinen Teil im Gesamtablauf so weit wie möglich optimieren. Dies führt zu einer Steigerung des Profits der gesamten Produktion und zu einer Steigerung des Einkommens aller ihrer Beschäftigten. Jetzt wurde der Staffelstab der Einführung des "5C"-Systems von Unternehmen auf der ganzen Welt übernommen, einschließlich Russland. In diesem Artikel werden wir versuchen, Skeptiker davon zu überzeugen, dass japanisches Know-how wirklich funktioniert, und zwar in jedem Tätigkeitsbereich.
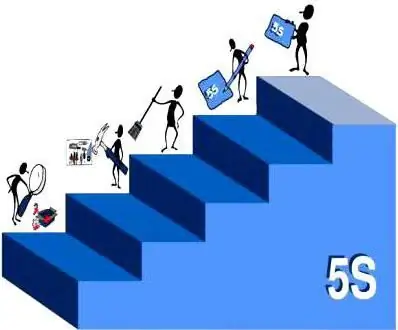
Das "5C"-System in der Produktion, was ist das
International 5S steht für fünf Schritte ("step" im englischen step). Einige Ökonomen und Befürworter eines neuen Arbeitsgefühls erklären den Namen mit den fünf japanischen Postulaten, die im 5S-System konsequent umgesetzt werden: Seiri, Seiton, Seiso, Seiketsu und Shitsuke. Für uns sind unsere einheimischen "5Cs" näher und verständlicher - fünf aufeinanderfolgende Schritte, die abgeschlossen werden müssen, um den Wohlstand unserer Produktion zu erreichen. Das ist:
1. Sortieren.
2. Ordnung h alten.
3. Sauber h alten.
4. Standardisierung.
5. Verbesserung.
Wie Sie sehen können, erfordert das "5C"-System nichts Übernatürliches in der Produktion. Vielleicht trifft man deshalb ihr gegenüber immer noch auf Misstrauen und Leichtfertigkeit.
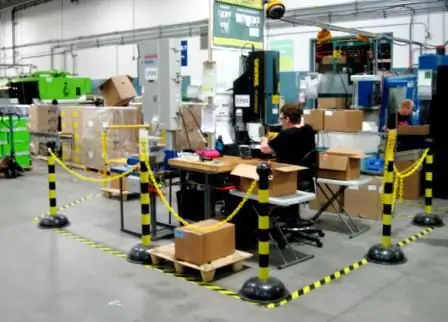
Phasen der Erstellung eines Systems
Der weise Japaner Taiichi Ohno, der es dank der Einführung seiner Methoden im Toyota-Werk geschafft hat, aufzusteigenIngenieur zum CEO, bemerkte, wie viele Verluste durch verschiedene Inkonsistenzen und Überlagerungen entstehen. Beispielsweise wurden einige kleine Schrauben nicht rechtzeitig auf das Förderband gelegt, wodurch die gesamte Produktion gestoppt wurde. Oder umgekehrt, die Teile wurden mit einer Marge geliefert, sie stellten sich als überflüssig heraus und infolgedessen musste einer der Mitarbeiter sie zurück ins Lager bringen, was bedeutet, dass sie ihre Zeit mit Leerarbeit verschwenden. Taiichi Ohno entwickelte ein Konzept, das er „just in time“nannte. Das heißt, es wurden jetzt genau so viele Teile wie nötig an das Förderband geliefert.
Weitere Beispiele könnten gegeben werden. Das „5S“-System in der Produktion umfasste auch das Konzept „Kanban“, was auf Japanisch „Werbeschild“bedeutet. Taiichi Ohno schlug vor, an jedem Teil oder jedem Werkzeug ein sogenanntes „Kanban“-Etikett anzubringen, in dem alle notwendigen Informationen zum Teil oder Werkzeug angegeben sind. Im Grunde gilt es für alles. Zum Beispiel an Waren, Medikamenten, Ordnern im Büro. Das dritte Konzept, auf dem das 5S-System in der Produktion basiert, ist das Konzept des „Kaizen“, was kontinuierliche Verbesserung bedeutet. Es wurden auch andere Konzepte erdacht, die nur für hochspezialisierte Produktionsprozesse geeignet waren. In diesem Artikel werden wir sie nicht berücksichtigen. Als Ergebnis aller in der Praxis erprobten Neuerungen haben sich 5 Schritte herausgebildet, die auf jede Produktion anwendbar sind. Analysieren wir sie im Detail.
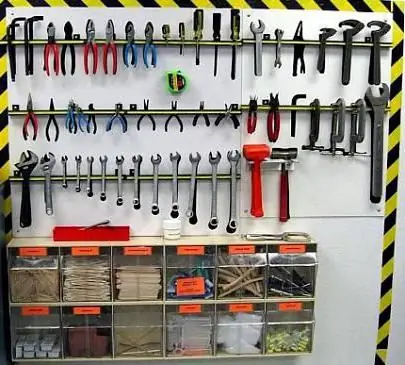
Sortierung
Viele von uns haben Elemente auf ihren Desktops, die ingrundsätzlich nicht nötig. Zum Beispiel alte Formulare, unbenutzte Akten, Berechnungsentwürfe, eine Serviette, auf der eine Tasse Kaffee stand. Und in diesem Chaos können sich die notwendigen Dateien oder Dokumente befinden. Die Grundprinzipien des „5S“-Systems bestehen darin, Ihren Arbeitsablauf zu optimieren, dh dafür zu sorgen, dass keine Zeit verschwendet wird, um das Richtige zwischen den Trümmern des Unnötigen zu suchen. Das ist sortieren. Das heißt, am Arbeitsplatz (neben der Maschine, auf dem Tisch, in der Werkstatt - überall) werden alle Gegenstände in zwei Stapeln ausgelegt - das Notwendige und das Unnötige, das entsorgt werden muss. Außerdem wird alles, was Sie brauchen, in die folgenden Stapel zerlegt: „häufig und ständig verwendet“, „selten verwendet“, „fast nicht verwendet“. Damit ist die Sortierung abgeschlossen.
Ordnung h alten
Wenn du die Gegenstände einfach zerlegst, hat das keinen Sinn. Es ist notwendig, diese Gegenstände (Werkzeuge, Unterlagen) so anzuordnen, dass das, was ständig und oft gebraucht wird, im Blickfeld ist, bzw. schnell mitgenommen und leicht wieder verstaut werden kann. Was selten verwendet wird, kann irgendwo in einer Kiste verschickt werden, aber es muss ein Kanban-Etikett angebracht werden, damit es nach einer Weile leicht und genau gefunden werden kann. Wie Sie sehen, beginnt das 5S-System am Arbeitsplatz mit den einfachsten Schritten, erweist sich aber tatsächlich als sehr effektiv. Außerdem verbessert es die Stimmung und den Arbeitswillen.
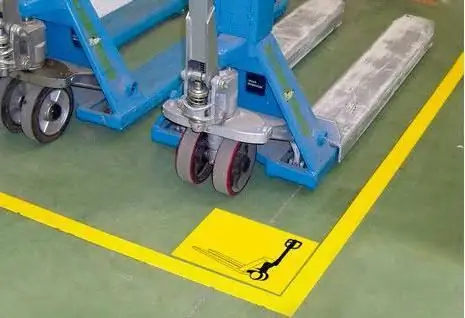
Sauber bleiben
Dieser dritte Schritt ist für viele der logischste. Von Kindheit an wird uns beigebracht, clean zu sein. Auf derAuch in der Produktion ist es notwendig, und nicht nur die Tische von Büroangestellten oder Schränke in Gastronomiebetrieben, sondern auch Maschinen, Hauswirtschaftsräume von Reinigungskräften sollten sauber sein. In Japan kümmern sich die Mitarbeiter gut um ihre Arbeitsplätze, sie werden dreimal täglich gereinigt - morgens vor der Arbeit, mittags und abends nach Feierabend. Darüber hinaus haben ihre Unternehmen eine spezielle Markierung von Bereichen eingeführt, die es ihnen ermöglichen, die Reihenfolge in der Produktion zu beobachten, d. h. Bereiche mit fertigen Produkten, Lagerung bestimmter Teile usw. sind mit unterschiedlichen Farben gekennzeichnet.
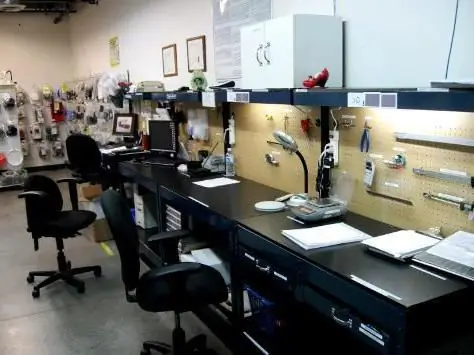
Standardisierung
Die Prinzipien der Standardisierung wurden von Taiichi Ohno erfunden. Sie werden auch häufig vom modernen 5S-System verwendet. Das Produktionsmanagement erhält dank der Standardisierung ein wunderbares Werkzeug zur Steuerung aller Prozesse. Dadurch werden die Ursachen für Terminverzögerungen schnell beseitigt und Fehler, die zur Freigabe minderwertiger Produkte führen, behoben. Im Werk von Toyota Motor sah die Standardisierung so aus: Meister erstellten Tagesarbeitspläne, am Arbeitsplatz hingen genaue Anweisungen und am Ende des Arbeitstages kontrollierten Spezialarbeiter, welche Abweichungen vom Plan während des Tages auftraten und warum. Dies ist die Grundregel der Standardisierung, dh präzise Anweisungen, Arbeitspläne und Kontrolle über deren Umsetzung. Jetzt führen viele Unternehmen, zum Beispiel ENSTO-Werke in Estland, ein Bonussystem für Mitarbeiter ein, die sich strikt an die Bestimmungen des 5C-Systems h alten und auf dieser Grundlage ihre Produktivität steigernist ein großer Anreiz, dieses System als Lebensweise anzunehmen.
Verbesserung
Der fünfte Schritt, der das „5S“-System in der Produktion vervollständigt, basiert auf dem Konzept von Kaizen. Das bedeutet, dass alle Mitarbeiter unabhängig von ihrer Position bestrebt sein sollten, den Arbeitsprozess in dem ihnen anvertrauten Bereich zu verbessern. Die philosophische Essenz von Kaizen ist, dass unser ganzes Leben jeden Tag besser wird, und da die Arbeit ein Teil des Lebens ist, sollte sie sich auch nicht von Verbesserungen fernh alten.
Das Betätigungsfeld ist hier breit, denn Perfektion kennt keine Grenzen. Nach den Vorstellungen der Japaner sollten die Arbeiter ihren Produktionsprozess selbst verbessern wollen, ohne Anweisungen oder Zwang. Heutzutage bilden viele Unternehmen Teams aus Mitarbeitern, die die Produktqualität überwachen, ihre positiven Erfahrungen an andere weitergeben und dabei helfen, Spitzenleistungen zu erzielen.
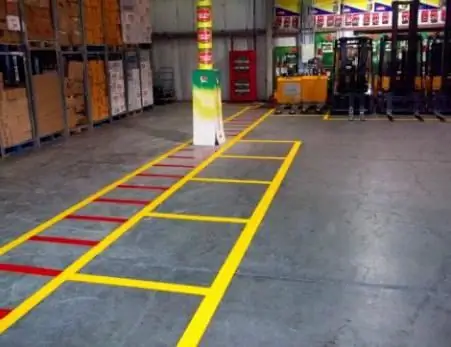
Grundlegende Fehler
Damit das „5C“-System funktioniert, reicht es nicht aus, es zu organisieren oder Mitarbeiter einzustellen, die ihre Kollegen dazu zwingen, es umzusetzen. Es ist wichtig, dass die Menschen den Nutzen dieser Innovation erkennen und sie als Lebensstil akzeptieren. Die Einführung des „5S“-Systems in Russland in der Produktion steht vor Schwierigkeiten, gerade weil unsere russische Mentalität anders ist als die japanische. Viele unserer Produktionen zeichnen sich durch folgendes aus:
1. Mitarbeiter, insbesondere wenn es keine Anreize für sie gibt, streben nicht danach, den Gewinn des Unternehmens zu steigern. Sie fragen,Warum versuchen, den Chef noch reicher zu machen, wenn er schon alles hat.
2. Die Verantwortlichen selbst haben kein Interesse an der Einführung des „5S“-Systems, weil sie darin keine Zweckmäßigkeit sehen.
3. Viele Anweisungen "von oben nach unten" sind gewohnt, nur für "Tick" auszuführen. In Japan gibt es eine ganz andere Einstellung zu ihrer Arbeit. Zum Beispiel dachte derselbe Taiichi Ohno bei der Einführung des "5S"-Systems nicht an persönlichen Gewinn, sondern an den Nutzen des Unternehmens, in dem er nur Ingenieur war.
4. In vielen Unternehmen wird das 5S-System zwangsweise eingeführt. Schlanke Produktion, die die Eliminierung von Verlusten aller Art (Arbeitszeit, Rohstoffe, gute Mitarbeiter, Motivation und andere Indikatoren) impliziert, funktioniert nicht, da die Arbeiter beginnen, sich Innovationen auf einer unbewussten Ebene zu widersetzen, was letztendlich alle Anstrengungen auf Null reduziert.
5. Manager, die das System implementieren, verstehen sein Wesen nicht vollständig, was zu Fehlern in etablierten Produktionsprozessen führt.
6. Standardisierung entwickelt sich oft zu Bürokratie, eine gute Tat wird überwuchert mit Anweisungen und Weisungen, die die Arbeit nur stören.
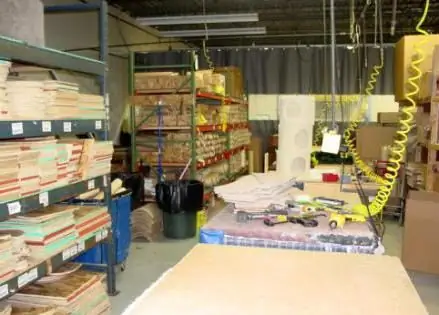
Bewertungen
Russen, die das "5S"-System in der Produktion eingeführt haben, ist das Feedback zu dieser Innovation sehr zweideutig. Hervorgehobene Vorteile:
- besser am Arbeitsplatz sein;
- nicht mit unnötigen Kleinigkeiten von der Arbeit ablenken;
- klarerer Arbeitsablauf;
- Müdigkeit am Ende der Schicht abgenommen;
- leicht erhöhtGeh alt durch Steigerung der Arbeitsproduktivität;
- Arbeitsunfälle zurückgegangen.
Nachteile:
- beim Sortieren zwingen sie alles wegzuwerfen;
- Standardisierung hat zu einem Anstieg der Bürokratie geführt;
- Die Einführung des „5C“-Systems hat die Probleme in allen Unternehmensbereichen nicht verschärft;
- Das 5S-System an erster Stelle zu setzen, hat wichtige Probleme wie den Mangel an Ersatzteilen überschattet.
Empfohlen:
Immobilienentwicklung und ihre Rolle in der wirtschaftlichen Entwicklung. Das Konzept, Typen, Prinzipien und Grundlagen der Entwicklung
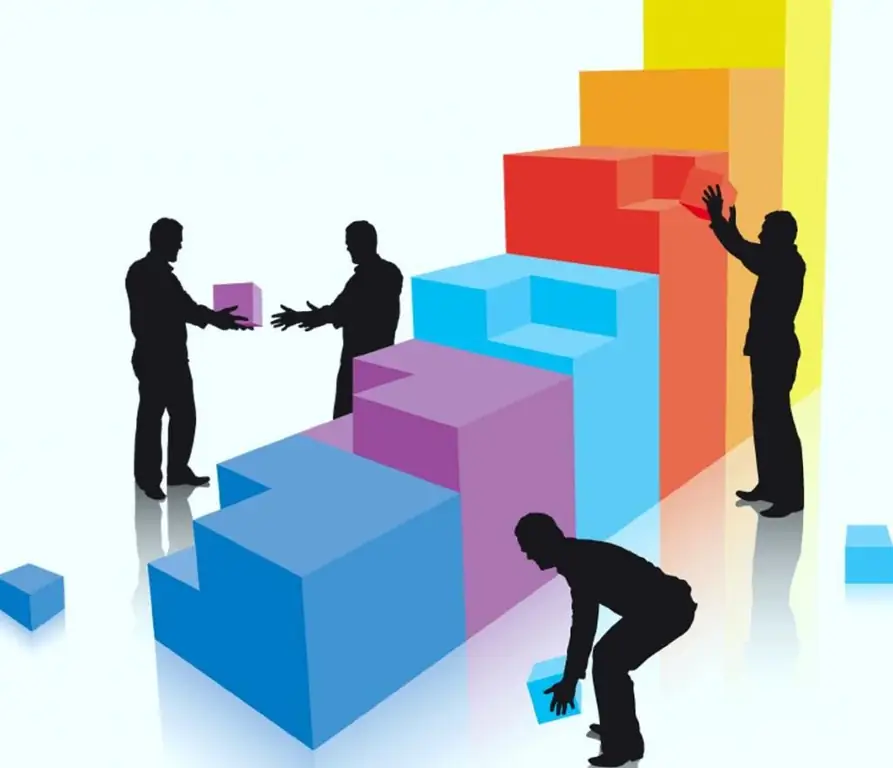
Im Rahmen dieses Artikels werden wir die Organisation des Immobilienentwicklungssystems und seine Rolle in der wirtschaftlichen Entwicklung betrachten. Es werden die grundlegenden Konzepte, Arten und Prinzipien der Organisation des Entwicklungssystems betrachtet. Die charakteristischen Merkmale des Systems unter russischen Bedingungen werden berücksichtigt
Geldpolitik der Zentralbank der Russischen Föderation: Merkmale, Ziele, Prinzipien der Schöpfung
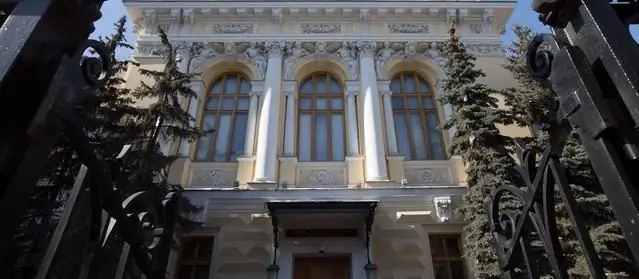
Die Führung der russischen Zentralbank verfolgt routinemäßig ein schwer vorhersagbares und gleichzeitig leicht zu analysierendes Modell der Regulierung der Währungsbeziehungen. Die obige Struktur positioniert sich als der größte Teilnehmer am Finanzmarkt, der keine klare und verständliche Strategie bei der Entwicklung von Mechanismen hat, durch die die nationale Wirtschaft verw altet wird
Der Hauptzweck der Budgetierung. Das Konzept, das Wesen des Prozesses und die Aufgaben der Budgetierung

Was ist der Hauptzweck der Budgetierung? Warum findet dieser Prozess statt? Warum wird es benötigt? Welche Aufgaben werden ausgeführt? Was ist das Wesen dieses Prozesses? Wie ist das Gesamtsystem aufgebaut? Diese, sowie eine Reihe weiterer Fragen, werden im Rahmen des Artikels beantwortet
Moderne Produktion. Die Struktur der modernen Produktion. Probleme der modernen Produktion

Eine entwickelte Industrie und ein hohes Niveau der Wirtschaft des Landes sind Schlüsselfaktoren, die den Wohlstand und das Wohlergehen seiner Bevölkerung beeinflussen. Ein solcher Staat hat große wirtschaftliche Chancen und Potenziale. Ein wesentlicher Bestandteil der Wirtschaft vieler Länder ist die Produktion
Ideen Mini-Produktion. Mini-Shop für kleine Unternehmen. Produktion in der Garage
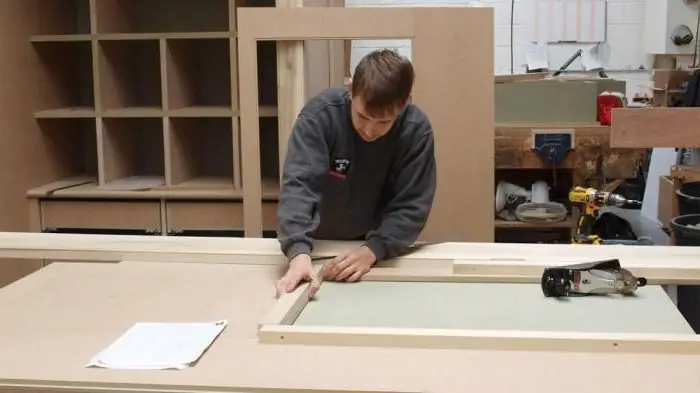
Was kann zu Hause oder in der Garage produziert werden? Wir organisieren Ihr Unternehmen von Grund auf mit minimalen Investitionen