2025 Autor: Howard Calhoun | [email protected]. Zuletzt bearbeitet: 2025-06-01 07:13
In der Fertigungs- und Bauindustrie ist die zerstörungsfreie Prüfung eine der beliebtesten Methoden zur Diagnose von Materialien. Mit dieser Methode bewerten Bauherren die Qualität von Schweißverbindungen, überprüfen die Dichte in bestimmten Abschnitten von Strukturen und decken tiefe Defekte und Fehler auf. Diagnostische magnetische Fehlersuchgeräte können sowohl oberflächliche als auch unterirdische Schäden mit hoher Genauigkeit erkennen.
Gerät Gerät
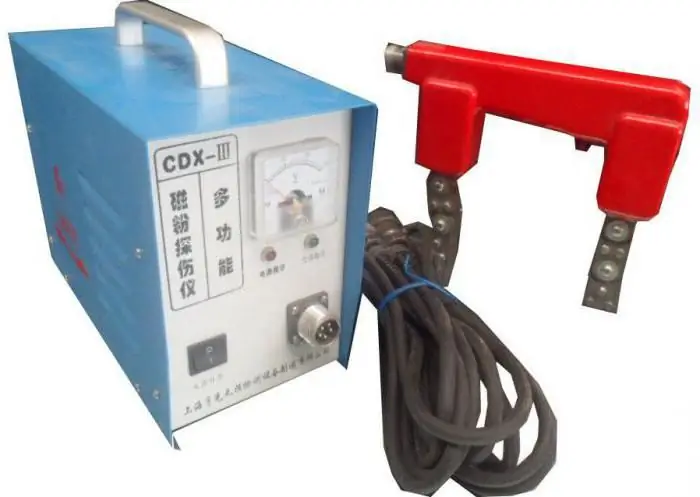
Basis des Segments der magnetischen Dicken- und Fehlerprüfgeräte sind Handgeräte, die mit magnetisierbaren Arbeitskörpern - meist in Form von Zangen - versehen sind. Äußerlich sind dies kleine Geräte, deren Füllung ein Elektromagnet ist, der die Pole der Wellenbewegung reguliert. Die Mittelklasse ermöglicht das Arbeiten mit magnetischer Permeabilität, deren Koeffizient höher als 40 ist. Der Körper ist mit einem ergonomischen Griff ausgestattet, dank dessen das Gerät an schwer zugänglichen Stellen eingesetzt werden kann. Zur Stromversorgung sind die Geräte außerdem mit einem Kabel versehen, das entweder an eine Generatorstation (bei Arbeiten im Freien) oder an ein 220-V-Haush altsnetz angeschlossen isthat eine stationäre Basis, die mit einem Computer verbunden ist. Solche Diagnosetools werden häufiger verwendet, um die Qualität von hergestellten Teilen in der Produktion zu überprüfen. Sie führen Qualitätskontrollen durch und beheben die kleinsten Abweichungen von den Standardindikatoren.
Ferroprobe-Prüfgeräte
Eine Vielzahl magnetischer Geräte zur Erkennung von Fehlern in einer Tiefe von bis zu 10 mm. Insbesondere werden sie verwendet, um Diskontinuitäten in der Struktur von Strukturen und Teilen zu beheben. Dies können Sonnenuntergänge, Muscheln, Risse und Haarlinien sein. Die Fluxgate-Methode wird auch zur Beurteilung der Qualität von Schweißnähten verwendet. Nach Beendigung der Arbeitssitzung können Magnetprüfgeräte dieser Art im Rahmen einer komplexen Diagnostik auch den Entmagnetisierungsgrad des Bauteils ermitteln. Hinsichtlich der Anwendung auf Teile unterschiedlicher Form und Größe sind den Geräten praktisch keine Grenzen gesetzt. Aber auch hier sollte man die maximale Tiefe der Strukturanalyse nicht vergessen.
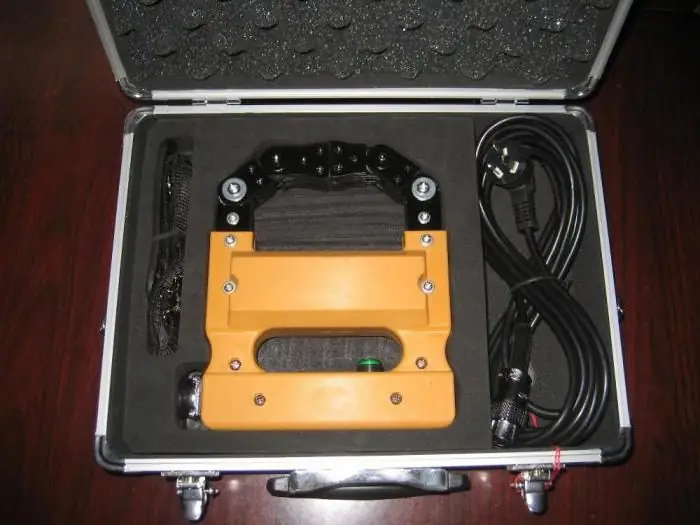
Magnitographische und Wirbelstromprüfgeräte
Mit Hilfe magnetografischer Geräte kann der Bediener Produktfehler in einer Tiefe von 1 bis 18 mm erkennen. Und auch hier sind Ungänzen und Defekte in Schweißnähten die Zielanzeichen für Abweichungen im Gefüge. Zu den Merkmalen der Wirbelstromprüftechnik gehört die Analyse der Wechselwirkung des elektromagnetischen Feldes mit den durch Wirbelströme erzeugten Wellen, die dem Prüfgegenstand zugeführt werden. Am häufigsten wird ein Wirbelstromprüfgerät zur Untersuchung von Produkten aus elektrisch leitfähigen Materialien eingesetzt. Geräte dieser Artzeigen ein sehr genaues Ergebnis bei der Analyse von Teilen mit aktiven elektrophysikalischen Eigenschaften, aber es ist wichtig zu berücksichtigen, dass sie in einer geringen Tiefe arbeiten - nicht mehr als 2 mm. Was die Art der Defekte betrifft, so ermöglicht die Wirbelstrommethode das Erkennen von Unterbrechungen und Rissen.
Magnetpulverprüfgeräte
Solche Geräte konzentrieren sich auch hauptsächlich auf Oberflächenfehler, die in einer Tiefe von bis zu 1,5-2 mm behoben werden können. Gleichzeitig wird die Möglichkeit der Forschung eingeräumt, eine breite Palette von Fehlern aufzudecken - von den Parametern der Schweißnaht bis zur Erkennung von Anzeichen von Delamination und Mikrorissen. Das Funktionsprinzip solcher zerstörungsfreier Prüfgeräte basiert auf der Aktivität von Pulverpartikeln. Unter Einwirkung eines elektrischen Stroms werden sie auf die Inhomogenität magnetischer Schwingungen gerichtet. Dadurch können Sie die Unvollkommenheiten der Oberfläche des Zielobjekts der Untersuchung beheben.
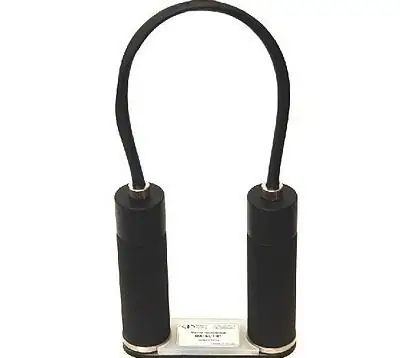
Die höchste Genauigkeit bei der Bestimmung defekter Bereiche mit dieser Methode ist gegeben, wenn die Ebene des defekten Bereichs einen 90-Grad-Winkel mit der Richtung des magnetischen Flusses bildet. Wenn wir von diesem Winkel abweichen, nimmt auch die Empfindlichkeit des Instruments ab. Bei der Arbeit mit solchen Geräten werden auch zusätzliche Werkzeuge verwendet, um die Fehlerparameter zu beheben. So ist beispielsweise das magnetische Prüfgerät „Magest 01“in der Grundausstattung mit einer Doppellupe und einem UV-Blitzlicht ausgestattet. Das heißt, die direkte Feststellung des Fehlers auf der Oberfläche erfolgt durch den Bediener durch Sichtprüfung.
Arbeitsvorbereitung
Vorbereitende Aktivitäten können in zwei Gruppen eingeteilt werden. Die erste umfasst die direkte Vorbereitung der Arbeitsfläche und die zweite die Einrichtung des Geräts. Wie beim ersten Teil muss das Teil von Rost, verschiedenen Arten von Fett, Ölflecken, Schmutz und Staub gereinigt werden. Ein qualitativ hochwertiges Ergebnis kann nur auf einer sauberen und trockenen Oberfläche erzielt werden. Als nächstes wird das Fehlersuchgerät eingerichtet, wobei der wichtigste Schritt die Kalibrierung mit Verifizierung gegen Standards sein wird. Letztere sind Materialproben mit Mängeln, anhand derer die Richtigkeit der Ergebnisse der Geräteanalyse beurteilt werden kann. Außerdem können Sie je nach Modell den Arbeitstiefenbereich und die Empfindlichkeit festlegen. Diese Indikatoren hängen von den Aufgaben der Fehlererkennung, den Eigenschaften des zu untersuchenden Materials und den Fähigkeiten des Geräts selbst ab. Moderne Hightech-Prüfgeräte erlauben auch eine automatische Justierung nach vorgegebenen Parametern.
Teil magnetisieren
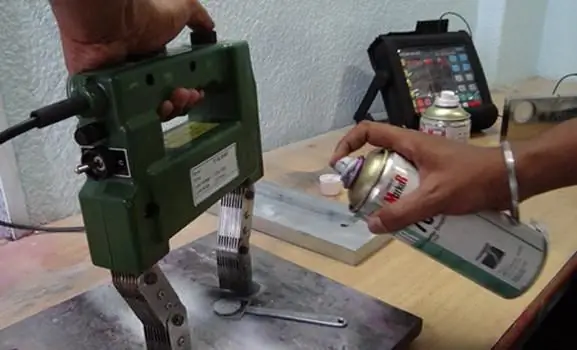
Die erste Phase des Arbeitsvorgangs, während der die Magnetisierung des zu untersuchenden Objekts durchgeführt wird. Zunächst ist es wichtig, die Strömungsrichtung und die Art der Magnetisierung mit Empfindlichkeitsparametern richtig zu bestimmen. Mit der Pulvermethode können Sie beispielsweise Stangen-, Kreis- und kombinierte Schläge auf das Teil ausführen. Insbesondere wird die kreisförmige Magnetisierung durchgeführt, indem ein elektrischer Strom direkt durch das Produkt, durch den Hauptleiter, durch die Wicklung oder durch einen separaten Abschnitt des Elements mit dem Anschluss elektrischer Schütze geleitet wird. BEIIm Polaktionsmodus stellen magnetische Fehlerdetektoren eine Magnetisierung unter Verwendung von Spulen, in einem Solenoidmedium, unter Verwendung eines tragbaren Elektromagneten oder unter Verwendung von Permanentmagneten bereit. Dementsprechend können Sie mit der kombinierten Methode zwei Methoden kombinieren, indem Sie zusätzliche Geräte beim Magnetisieren des Werkstücks anschließen.
Aufbringen eines magnetischen Indikators
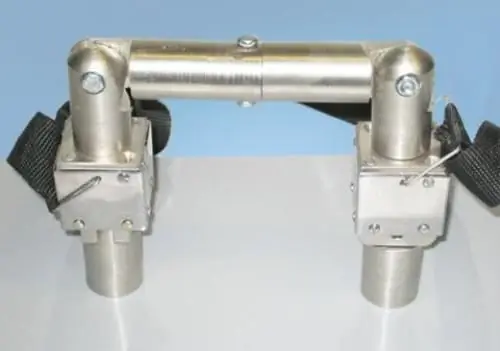
Indikatormaterial wird auf die vorbereitete und magnetisierte Oberfläche aufgetragen. Es ermöglicht Ihnen, die Fehler des Teils unter dem Einfluss eines elektromagnetischen Feldes zu identifizieren. Es wurde bereits gesagt, dass Pulver in dieser Funktion verwendet werden können, aber einige Modelle funktionieren auch mit Suspensionen. In beiden Fällen ist es wichtig, vor der Arbeit die optimalen Bedingungen für die Verwendung des Geräts zu berücksichtigen. Beispielsweise wird das magnetische Prüfgerät „MD-6“für den Einsatz bei Temperaturen von -40 bis 50 °C und einer Luftfeuchtigkeit bis 98 % empfohlen. Wenn die Bedingungen die Anforderungen für den Betrieb erfüllen, können Sie mit der Anwendung des Indikators beginnen. Das Puder wird flächendeckend aufgetragen - so dass auch eine geringe Abdeckung von nicht zum Studium vorgesehenen Stellen gegeben ist. Dadurch erh alten Sie ein genaueres Bild des Defekts. Die Suspension wird per Düse mit einem Schlauch oder Aerosol aufgetragen. Es gibt auch Verfahren zum Eintauchen des Teils in einen Behälter mit einer magnetischen Indikatormischung. Dann können Sie direkt mit der Fehlerbehebung des Produkts fortfahren.
Prüfteil
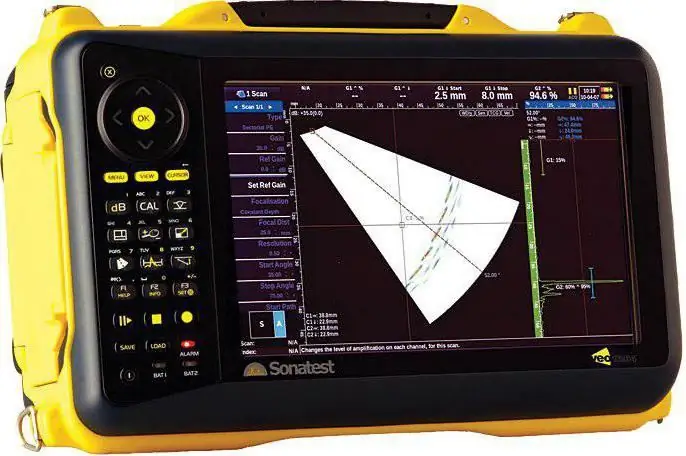
Der Bediener muss warten, bis die Aktivität des Indikators endet,seien es Pulverpartikel oder Suspension. Mit den vorgenannten Geräten in Form von optischen Geräten wird das Produkt visuell geprüft. In diesem Fall sollte die Vergrößerungsleistung dieser Geräte das 10-fache nicht überschreiten. Je nach Anforderung an die Untersuchung kann der Bediener auch bereits Bilder für eine genauere Computeranalyse erstellen. Multifunktionale magnetische Fehlerprüfstationen haben in ihrer Grundausstattung eine Ausrüstung zum Decodieren von Repliken mit Pulverablagerungen. Die bei der Sortierung erh altenen Zeichnungen werden anschließend mit Standardmustern verglichen, was uns einen Rückschluss auf die Qualität des Produktes und dessen Zulässigkeit für den vorgesehenen Verwendungszweck zulässt.
Schlussfolgerung
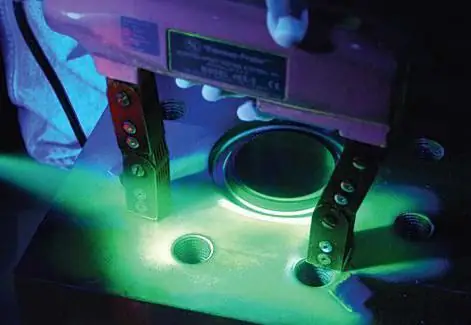
Instrumente zur magnetischen Fehlersuche sind in verschiedenen Bereichen weit verbreitet. Sie haben aber auch Nachteile, die ihren Einsatz einschränken. Dazu gehören je nach Betriebsbedingungen die Anforderungen an die Temperaturbedingungen und teilweise eine unzureichende Genauigkeit. Als universelles Kontrollmittel empfehlen Experten den Einsatz eines Mehrkanal-Magnetprüfgeräts, das auch in der Lage ist, die Funktion der Ultraschallanalyse zu unterstützen. Die Anzahl der Kanäle kann 32 erreichen. Das bedeutet, dass das Gerät in der Lage sein wird, optimale Fehlererkennungsparameter für die gleiche Anzahl unterschiedlicher Aufgaben aufrechtzuerh alten. Unter Kanälen versteht man im Wesentlichen die Anzahl der Betriebsmodi, die auf bestimmte Eigenschaften des Zielmaterials und der Umgebungsbedingungen ausgerichtet sind. Solche Modelle sind nicht billig, aber sie leistendie Richtigkeit der Ergebnisse bei der Erkennung von Oberflächenfehlern und inneren Strukturen verschiedener Art.
Empfohlen:
Glasofen: Typen, Gerät, Spezifikationen und praktische Anwendung
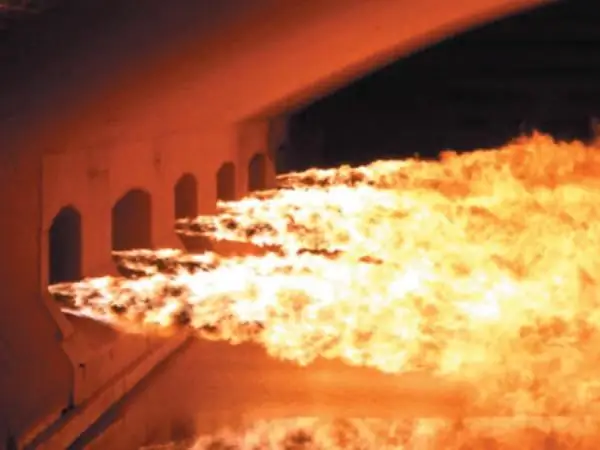
Heute verwenden Menschen Glas aktiv für eine Vielzahl von Zwecken. Der Glasherstellungsprozess selbst ist das Schmelzen von Rohstoffen oder Chargen. Zum Schmelzen des Materials werden Glasschmelzöfen verwendet. Sie kommen in verschiedenen Typen vor und werden nach mehreren Kriterien klassifiziert
Geschäftsidee: Unaufh altsame Baumstamm-Attraktion
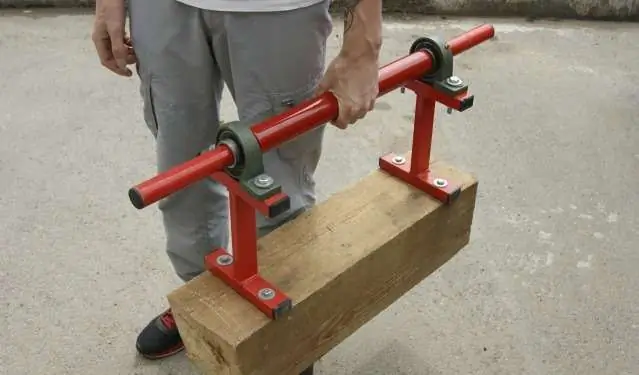
Attraktionen sind ein integraler Bestandteil aller Ferienorte der Welt. Darüber hinaus sind sie in fast allen Parks zu finden, auf Messen präsent usw. Zu den relativen Neuheiten gehört beispielsweise die Attraktion Unstoppable Log, bei der es fast unmöglich ist, einen Preis für eine Person mit durchschnittlichen körperlichen Fähigkeiten zu gewinnen. Diskutiert wird die Idee, genau so ein kleines Geschäft zu eröffnen
Mobile Tankstelle: Beschreibung, Gerät, Funktionsprinzip, Anwendung
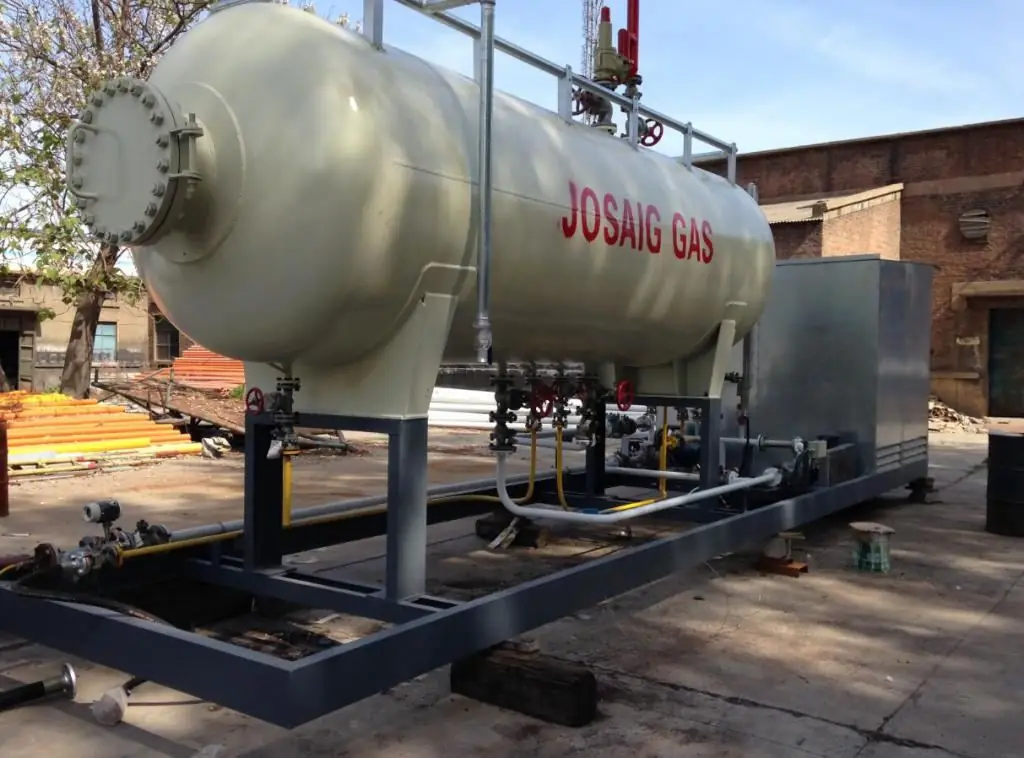
Mobile Tankstellen sind heutzutage eine beliebte Geschäftsidee. Daher kann das Erzielen von Erfolgen in diesem Bereich nur möglich sein, wenn Sie den verschiedenen Schlüsselpunkten, die in diesem Artikel beschrieben werden, maximale Aufmerksamkeit schenken
Absperrventile - was ist das? Gerät, Anwendung
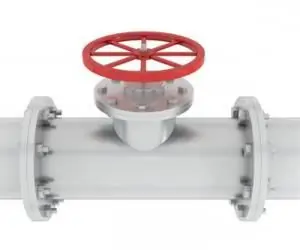
Der Begriff "Absperrventile" bezieht sich auf Geräte, die die Kraft des Flusses eines bestimmten Mediums steuern. Am häufigsten sind Ventilelemente an Rohrleitungen vorhanden. Als nächstes werden wir verstehen, in welche Arten von Ventilen unterteilt wird, was es ist und wo es verwendet wird
Zylinder "Rockwool" (Rockwool): Beschreibung, Gerät, Funktionsprinzip, Anwendung, Foto
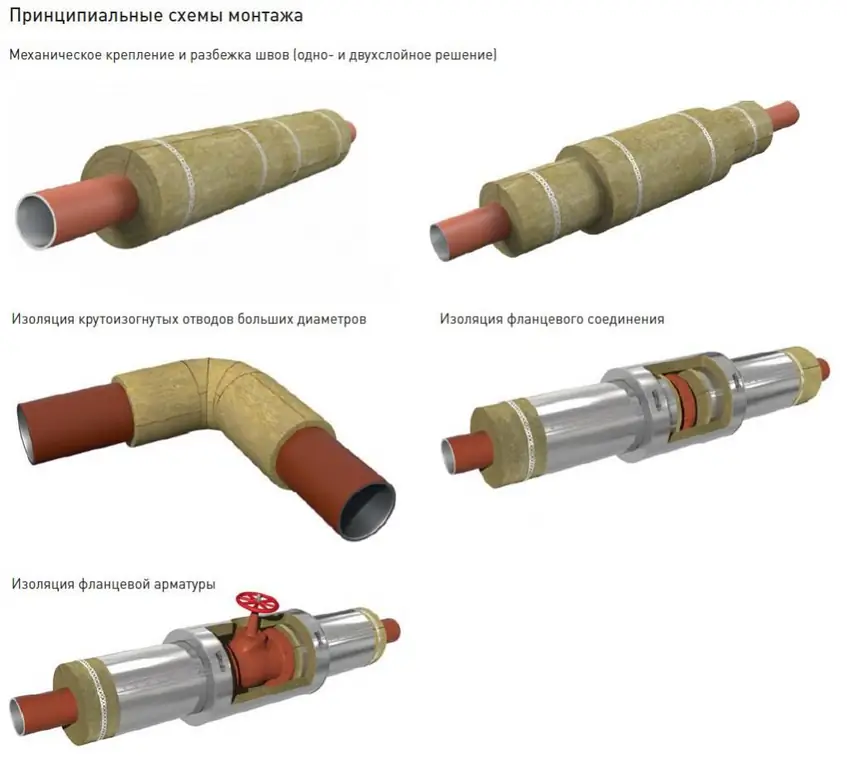
Die Lebensdauer von Rohren wird durch den Einsatz bei niedrigen Temperaturen und hoher Luftfeuchtigkeit reduziert. Dieses Problem kann jedoch durch den Einsatz moderner Schutzmaterialien aus Mineralwolle gelöst werden. Unter der großen Vielf alt an Angeboten auf dem Markt sind Zylinder von Rockwool nicht die letzten. Das Unternehmen begann seine Tätigkeit vor mehr als einem Jahrhundert in Dänemark. Während seiner Existenz hat es die Anerkennung der Verbraucher erreicht