2025 Autor: Howard Calhoun | [email protected]. Zuletzt bearbeitet: 2025-01-24 13:14
Die Effizienz und die Probleme der Plasmabeschichtung sind für Materialingenieure äußerst akut. Dank dieser Technologie ist es möglich, nicht nur die Lebensdauer und Zuverlässigkeit hochbelasteter Teile und Baugruppen deutlich zu erhöhen, sondern auch verschlissene und zerstörte Produkte scheinbar hundertprozentig wiederherzustellen.
Die Einführung der Plasmabeschichtung in den technologischen Prozess erhöht die Wettbewerbsfähigkeit von Maschinenbauprodukten erheblich. Das Verfahren ist nicht grundsätzlich neu und wird schon lange angewendet. Aber es verbessert und erweitert ständig seine technologischen Fähigkeiten.
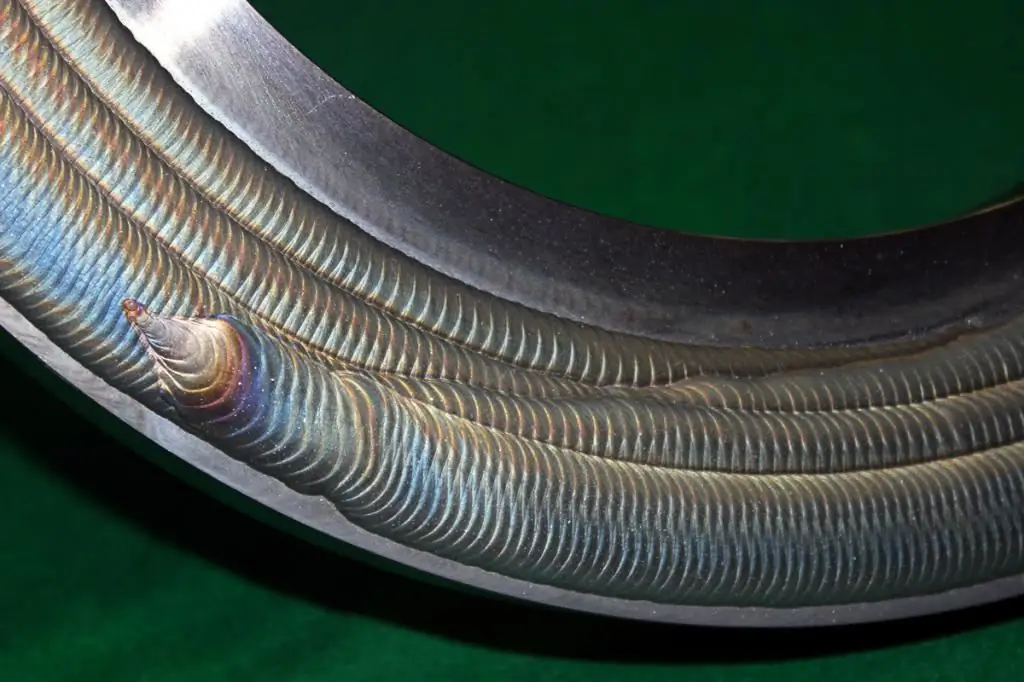
Allgemeine Bestimmungen
Plasma ist ein ionisiertes Gas. Es ist sicher bekannt, dass Plasma durch verschiedene Verfahren durch elektrische, thermische oder mechanische Einwirkung auf Gasmoleküle erh alten werden kann. Zu seiner Bildung ist es notwendig, negativ geladene Elektronen von positiven Atomen abzureißen.
In einigen Quellen findet manInformationen, dass Plasma neben fest, flüssig und gasförmig der vierte Aggregatzustand der Materie ist. Ionisiertes Gas hat eine Reihe nützlicher Eigenschaften und wird in vielen Bereichen der Wissenschaft und Technik verwendet: Plasmaauftragschweißen von Metallen und Legierungen zur Wiederherstellung und Härtung stark belasteter Produkte, die zyklischen Belastungen ausgesetzt sind, Ionen-Plasmanitrieren in einer Glimmentladung zur Diffusionssättigung und Härtung von Bauteiloberflächen, zur Durchführung chemischer Prozesse Beizen (Einsatz in der Elektronikfertigungstechnik).
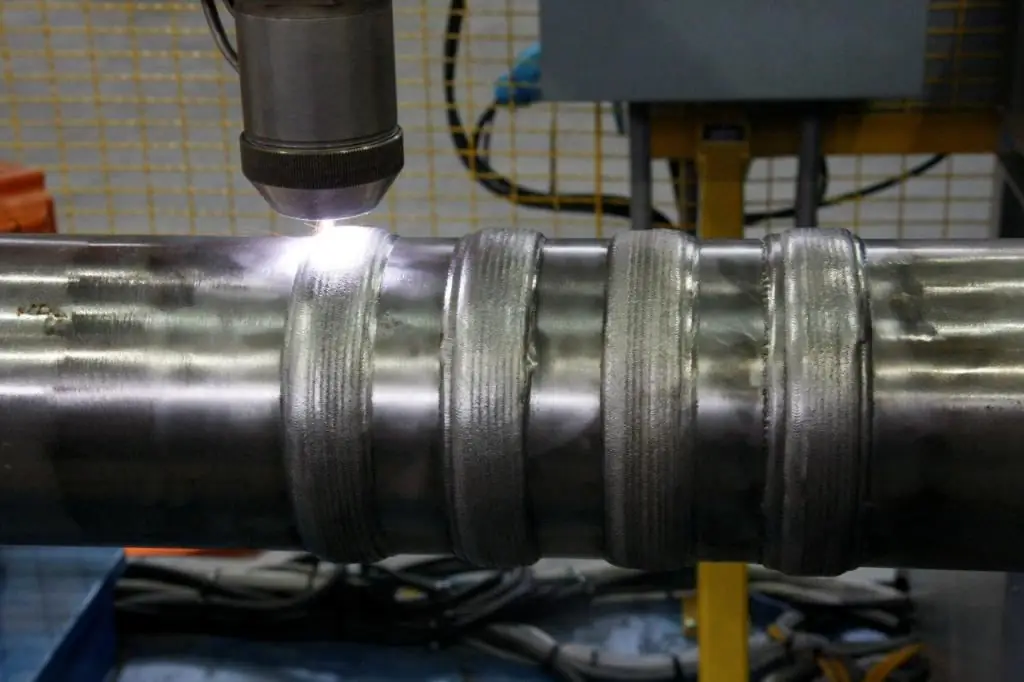
Arbeitsvorbereitung
Bevor du mit dem Auftauchen beginnst, musst du die Ausrüstung aufbauen. In Übereinstimmung mit den Referenzdaten ist es notwendig, den richtigen Neigungswinkel der Brennerdüse zur Oberfläche des Produkts auszuwählen und einzustellen, den Abstand vom Ende des Brenners zum Teil auszurichten (er sollte zwischen 5 und 8 betragen Millimeter) und Draht einführen (falls Drahtmaterial auftaucht).
Soll das Auftragen durch Schwankungen der Düse in Querrichtung erfolgen, so ist es notwendig, den Kopf so einzustellen, dass die Schweißnaht genau in der Mitte zwischen den Extrempunkten der Schwankungsamplituden der liegt Kopf. Es ist auch notwendig, den Mechanismus einzustellen, der die Frequenz und Größe der oszillierenden Bewegungen des Kopfes einstellt.
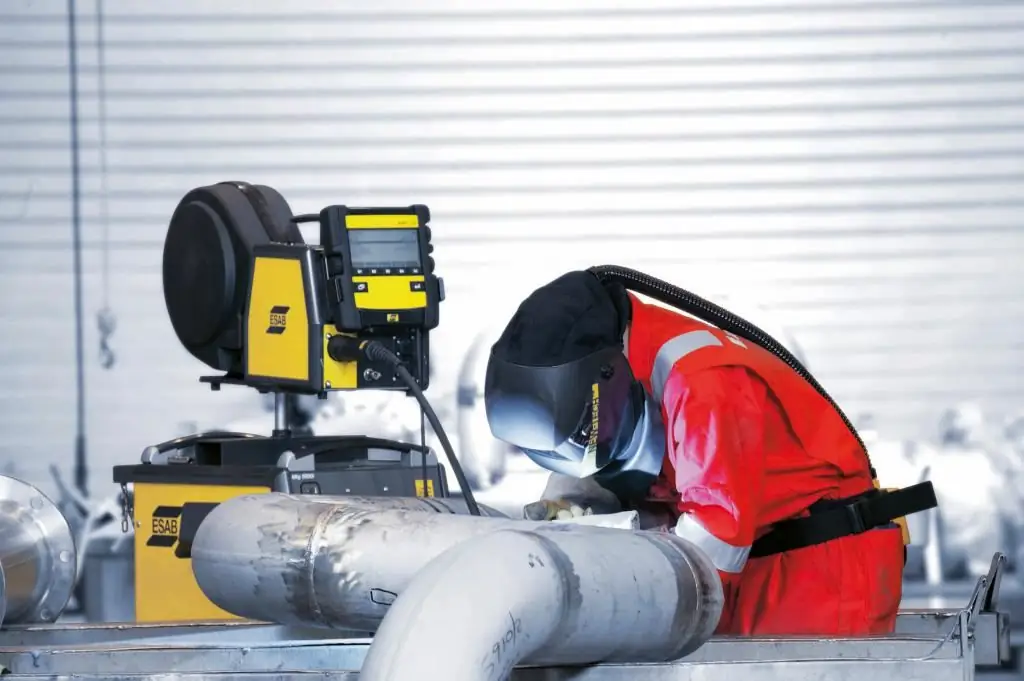
Plasmabogenbeschichtungstechnologie
Der Auftragprozess ist recht einfach und kann von jedem erfahrenen Schweißer erfolgreich durchgeführt werden. Allerdings verlangt erDarsteller von maximaler Konzentration und Aufmerksamkeit. Andernfalls können Sie das Werkstück leicht ruinieren.
Eine starke Bogenentladung dient zur Ionisierung des Arbeitsgases. Die Ablösung negativer Elektronen von positiv geladenen Atomen erfolgt durch die thermische Wirkung des Lichtbogens auf den Strahl des Arbeitsgasgemisches. Unter einer Reihe von Bedingungen ist der Fluss jedoch nicht nur unter dem Einfluss der thermischen Ionisation möglich, sondern auch aufgrund des Einflusses eines starken elektrischen Feldes.
Gas wird unter einem Druck von 20-25 Atmosphären zugeführt. Für seine Ionisierung wird eine Spannung von 120-160 Volt bei einer Stromstärke von etwa 500 Ampere benötigt. Positiv geladene Ionen werden vom Magnetfeld eingefangen und strömen zur Kathode. Die Geschwindigkeit und kinetische Energie von Elementarteilchen ist so groß, dass sie beim Zusammenstoß mit Metall eine enorme Temperatur erzeugen können - von +10 bis +18.000 Grad Celsius. Dabei bewegen sich die Ionen mit einer Geschwindigkeit von bis zu 15 Kilometern pro Sekunde (!). Die Plasmabeschichtungsanlage ist mit einem speziellen Gerät ausgestattet, das als "Plasmabrenner" bezeichnet wird. Es ist dieser Knoten, der für die Ionisation des Gases und den Erh alt eines gerichteten Stroms von Elementarteilchen verantwortlich ist.
Die Stärke des Lichtbogens sollte so groß sein, dass ein Schmelzen des Grundmaterials verhindert wird. Gleichzeitig sollte die Produkttemperatur möglichst hoch sein, um Diffusionsprozesse zu aktivieren. Daher sollte sich die Temperatur der Liquiduslinie im Eisen-Zementit-Diagramm annähern.
Fein Pulver einer speziellen Zusammensetzung oder Elektrodendraht wird in einen Strahl aus Hochtemperatur-Plasma geleitet, in dem sich das Material befindetschmilzt. Im flüssigen Zustand fällt der Belag auf die ausgehärtete Oberfläche.
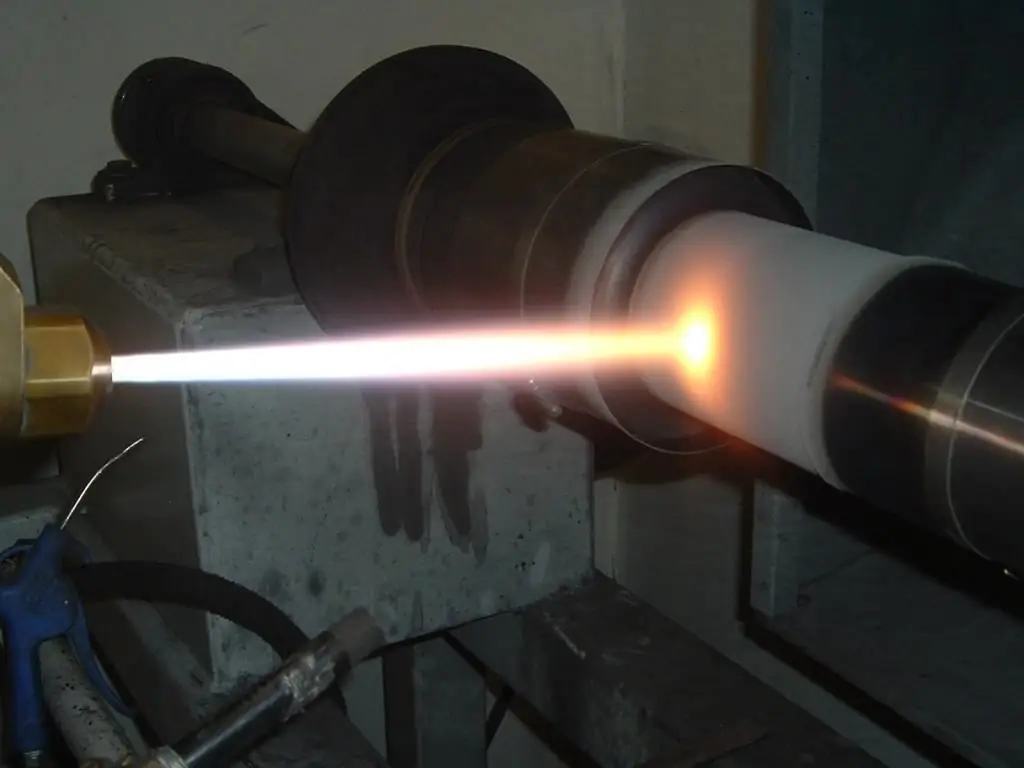
Plasmasprühen
Um das Plasmaspritzen zu realisieren, ist es notwendig, die Plasmaflussrate deutlich zu erhöhen. Dies kann durch Einstellen von Spannung und Strom erreicht werden. Parameter werden empirisch ausgewählt.
Materialien für das Plasmaspritzen sind Refraktärmetalle und chemische Verbindungen: Wolfram, Tantal, Titan, Boride, Silizide, Magnesiumoxid und Aluminiumoxid.
Der unbestreitbare Vorteil des Spritzens gegenüber dem Schweißen ist die Fähigkeit, die dünnsten Schichten in der Größenordnung von mehreren Mikrometern zu erh alten.
Diese Technologie wird zum Härten von Schneid-Dreh- und Fräs-Wechseleinsätzen aus Hartmetall sowie von Gewindebohrern, Bohrern, Senkern, Reibahlen und anderen Werkzeugen verwendet.
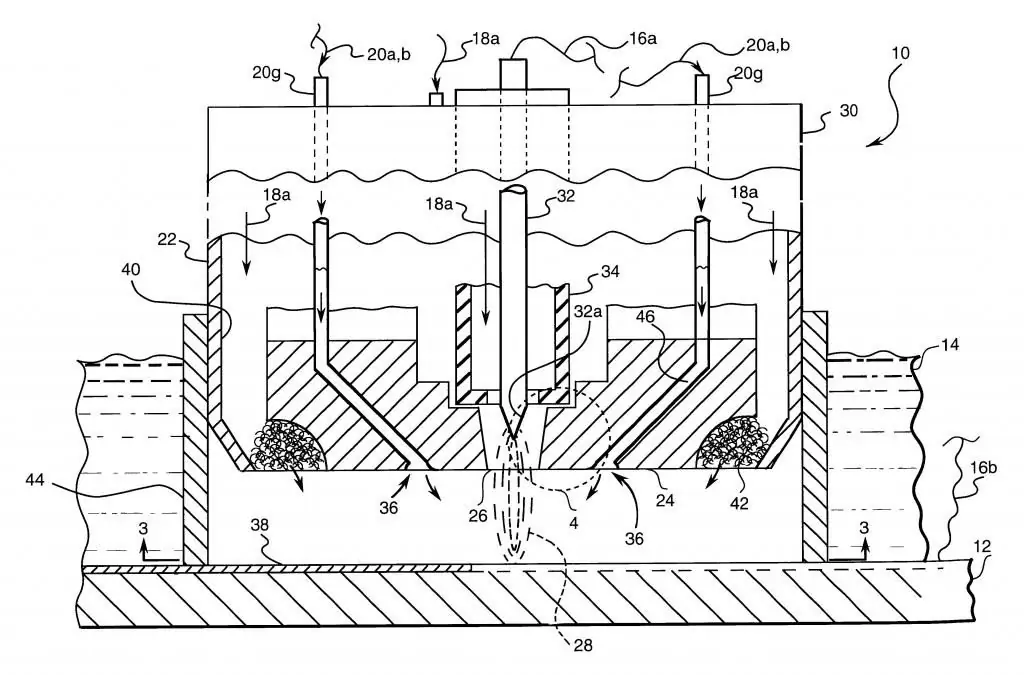
Gewinnung eines offenen Plasmastrahls
In diesem Fall fungiert das Werkstück selbst als Anode, auf der das Material durch Plasma abgeschieden wird. Der offensichtliche Nachteil dieser Verarbeitungsmethode ist die Erwärmung der Oberfläche und des gesamten Volumens des Teils, was zu strukturellen Veränderungen und unerwünschten Folgen führen kann: Erweichung, erhöhte Sprödigkeit usw.
Plasmadüse geschlossen
In diesem Fall wirkt der Gasbrenner, genauer gesagt seine Düse, als Anode. Dieses Verfahren wird für die Plasma-Pulver-Oberflächenbehandlung verwendet, um die Leistung von Teilen wiederherzustellen und zu verbessernMaschinenknoten. Besonders beliebt ist diese Technologie im Bereich der Landtechnik.
Vorteile des Plasmaauftragschweißens
Einer der Hauptvorteile ist die Konzentration der Wärmeenergie auf eine kleine Fläche, wodurch die Auswirkung der Temperatur auf die ursprüngliche Struktur des Materials reduziert wird.
Der Prozess ist gut überschaubar. Auf Wunsch und bei entsprechenden Geräteeinstellungen kann die Deckschicht von wenigen Zehntel Millimetern bis zu zwei Millimetern variieren. Die Möglichkeit, eine kontrollierte Schicht zu erh alten, ist derzeit besonders relevant, da sie es ermöglicht, die Wirtschaftlichkeit der Verarbeitung erheblich zu steigern und optimale Eigenschaften (Härte, Korrosionsbeständigkeit, Verschleißfestigkeit und viele andere) der Oberflächen von Stahlprodukten zu erzielen.
Ein weiterer, nicht weniger wichtiger Vorteil ist die Fähigkeit, Plasmaschweißen und Auftragen einer Vielzahl von Materialien durchzuführen: Kupfer, Messing, Bronze, Edelmetalle sowie Nichtmetalle. Herkömmliche Schweißverfahren sind dazu längst nicht immer in der Lage.
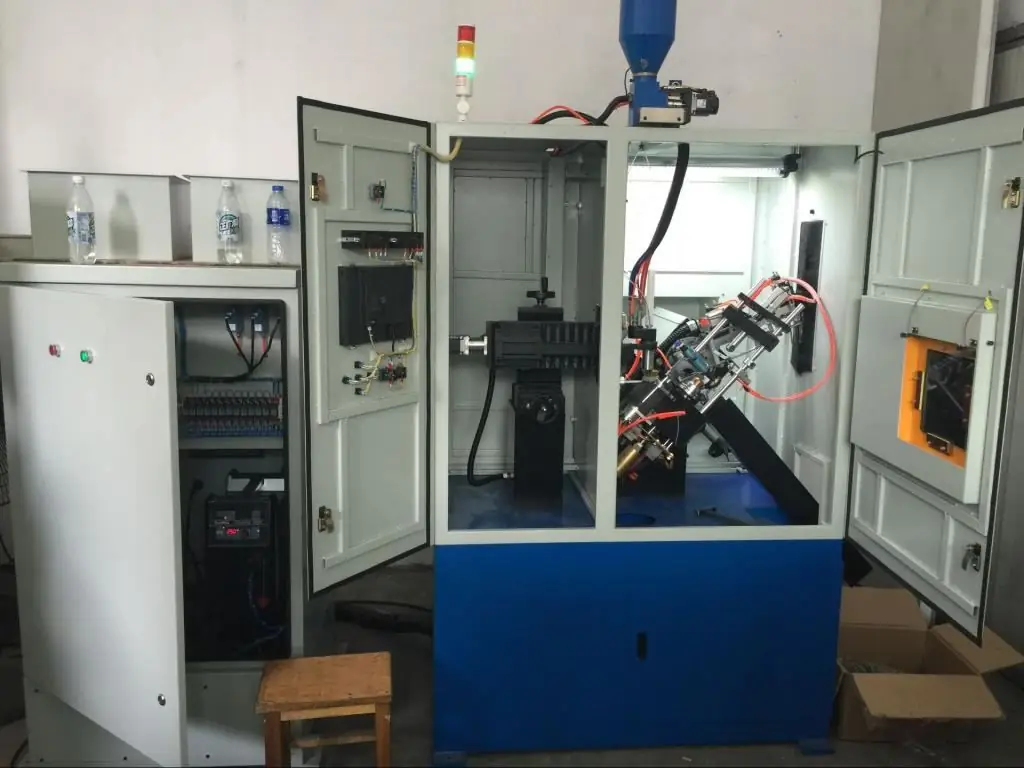
Hartauftragsausrüstung
Die Installation für die Plasmapulver-Oberflächenbehandlung umfasst eine Drossel, einen Oszillator, einen Plasmabrenner und Stromversorgungen. Außerdem sollte es mit einer Vorrichtung zum automatischen Zuführen von Metallpulvergranulat in den Arbeitsbereich und einem Kühlsystem mit ständiger Wasserzirkulation ausgestattet sein.
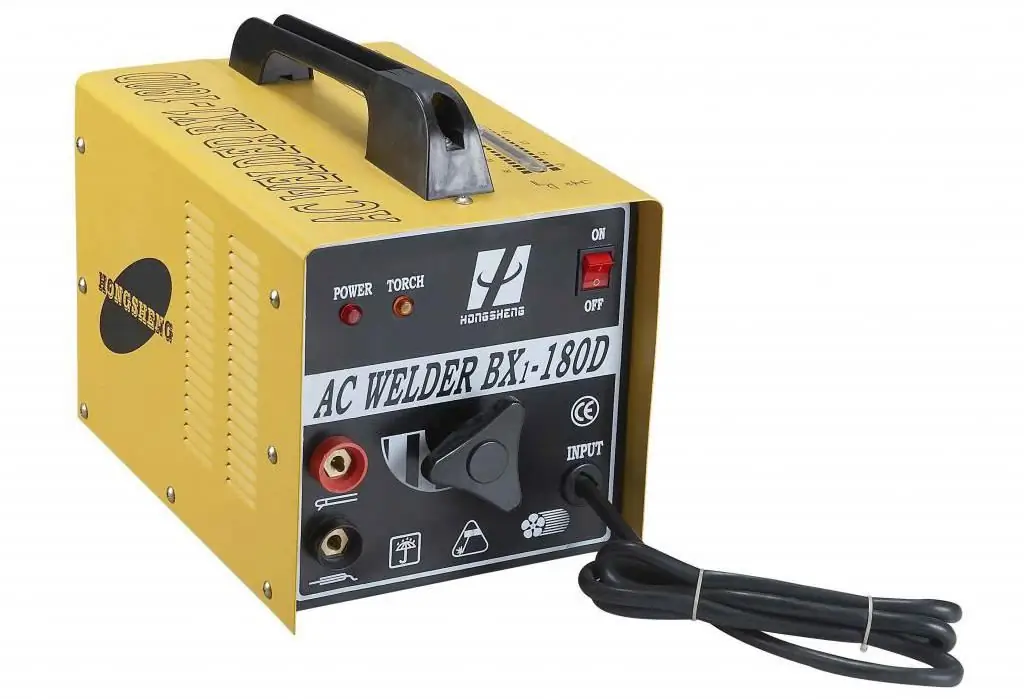
Stromquellen für das Plasmaauftragschweißen müssen strenge Anforderungen erfüllenBeständigkeit und Zuverlässigkeit. Schweißtransformatoren leisten mit dieser Rolle den besten Job.
Beim Auftragen von Pulvermaterialien auf eine Metalloberfläche wird der sogenannte kombinierte Lichtbogen verwendet. Sowohl offene als auch geschlossene Plasmastrahlen werden gleichzeitig verwendet. Durch Einstellen der Leistung dieser Lichtbögen ist es möglich, die Eindringtiefe des Werkstücks zu verändern. Unter optimalen Bedingungen treten keine Verwerfungen der Produkte auf. Dies ist wichtig bei der Herstellung von Teilen und Baugruppen der Feinwerktechnik.
Materialzufuhr
Metallpulver wird über eine spezielle Vorrichtung dosiert und der Schmelzzone zugeführt. Der Mechanismus oder das Funktionsprinzip des Dosierers ist wie folgt: Die Rotorblätter drücken das Pulver in den Gasstrom, die Partikel werden erhitzt und haften an der behandelten Oberfläche. Das Pulver wird durch eine separate Düse zugeführt. Insgesamt sind im Gasbrenner drei Düsen verbaut: für die Zufuhr von Plasma, für die Zufuhr von Arbeitspulver und für Schutzgas.
Wenn Sie Draht verwenden, ist es ratsam, den Standardvorschubmechanismus einer UP-Schweißmaschine zu verwenden.
Oberflächenvorbereitung
Der Plasmabehandlung und dem Besprühen von Materialien sollte eine gründliche Reinigung der Oberfläche von Fettflecken und anderen Verunreinigungen vorausgehen. Wenn beim konventionellen Schweißen nur eine grobe, oberflächliche Reinigung der Fugen von Rost und Zunder durchgeführt werden darf, muss beim Arbeiten mit Gasplasma die Oberfläche des Werkstücks ideal (möglichst) sauber und ohne Fremdeinschlüsse sein. Der dünnste Oxidfilm ist in der Lageschwächen die adhäsive Wechselwirkung zwischen der Hartauftragung und dem Grundmetall erheblich.
Um die Oberfläche für die Oberflächenbehandlung vorzubereiten, wird empfohlen, eine unbedeutende Oberflächenmetallschicht durch spanabhebende Bearbeitung und anschließendes Entfetten zu entfernen. Wenn es die Abmessungen des Teils zulassen, empfiehlt es sich, die Oberflächen in einem Ultraschallbad zu waschen und zu reinigen.
Wichtige Eigenschaften von Metalloberflächen
Es gibt mehrere Optionen und Methoden für die Plasmaoberflächenbildung. Die Verwendung von Draht als Auftragsmaterial erhöht die Produktivität des Prozesses gegenüber Pulvern deutlich. Dies liegt daran, dass die Elektrode (Draht) als Anode wirkt, was zu einer viel schnelleren Erwärmung des abgeschiedenen Materials beiträgt, wodurch Sie die Bearbeitungsmodi nach oben anpassen können.
Die Qualität der Beschichtung und die Haftungseigenschaften liegen jedoch eindeutig auf der Seite der Pulveradditive. Die Verwendung von feinen Metallpartikeln ermöglicht es, eine gleichmäßige Schicht beliebiger Dicke auf der Oberfläche zu erh alten.
Oberflächenpulver
Der Einsatz von Pulverauftragschweißen ist im Hinblick auf die Qualität der resultierenden Oberflächen und die Verschleißfestigkeit zu bevorzugen, daher werden in der Produktion zunehmend Pulvermischungen eingesetzt. Die traditionelle Zusammensetzung der Pulvermischung besteht aus Kob alt- und Nickelpartikeln. Die Legierung dieser Metalle hat gute mechanische Eigenschaften. Nach der Verarbeitung mit einer solchen Zusammensetzung bleibt die Oberfläche des Teils vollkommen glatt und es ist keine mechanische Nachbearbeitung und Beseitigung von Unregelmäßigkeiten erforderlich. Der Anteil der Pulverpartikel beträgt nur wenige Mikrometer.
Empfohlen:
Langfristige Anlagen sind Konzept, Arten, Eigenschaften und mögliche Risiken von langfristigen Anlagen
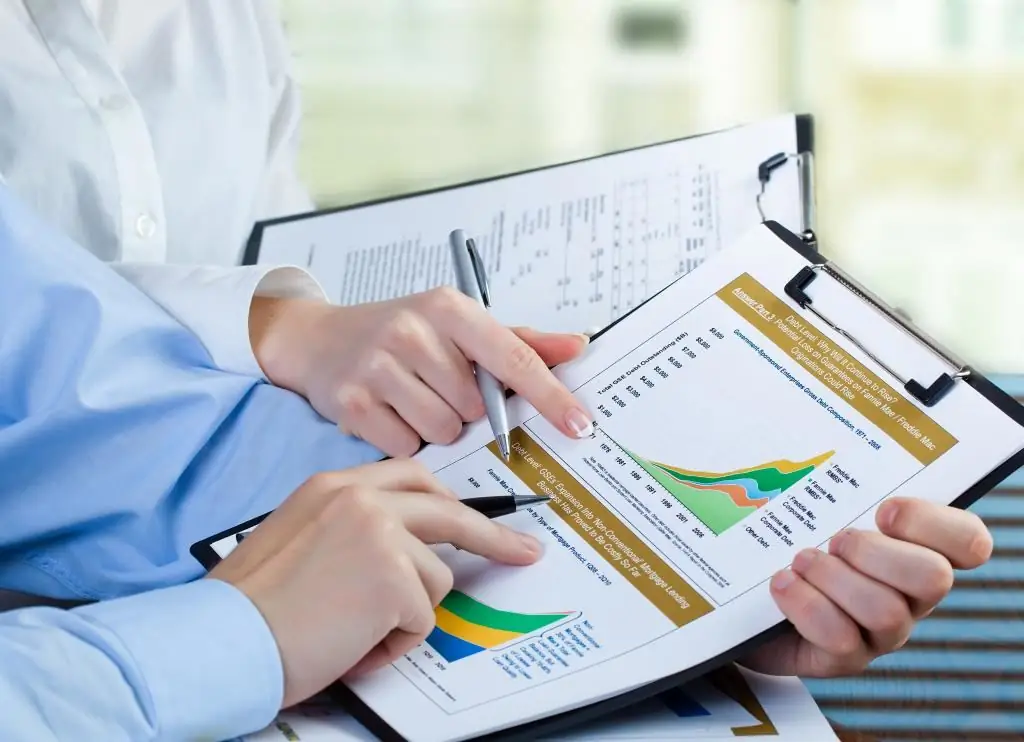
Ist es rentabel, Geld langfristig anzulegen? Gibt es Risiken für Anleger? Welche Arten von langfristigen Investitionen gibt es und wie wählt man die richtige Quelle für zukünftiges Einkommen? Welche Schritte sollte ein Anleger unternehmen, um Geld langfristig sicher und gewinnbringend anzulegen?
Müllsortieranlage: Anlagen zum Sortieren und Verarbeiten von Hausmüll
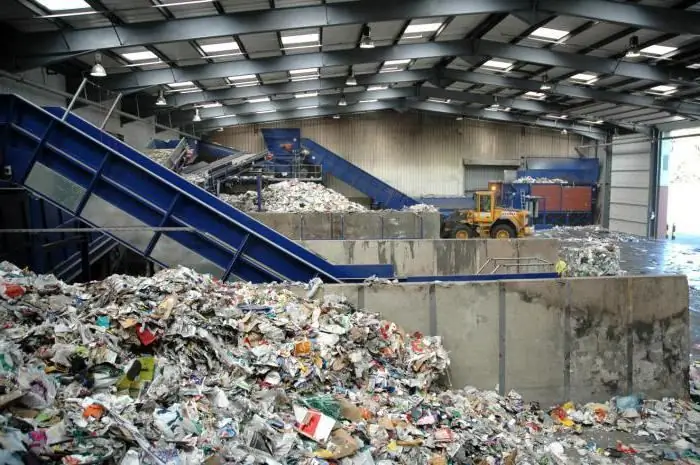
Der Artikel ist Abfallsortierkomplexen gewidmet. Die Merkmale dieser Ausrüstung, die durchgeführten technologischen Schritte usw. werden berücksichtigt
Renditestarke Anlagen: Wo investieren
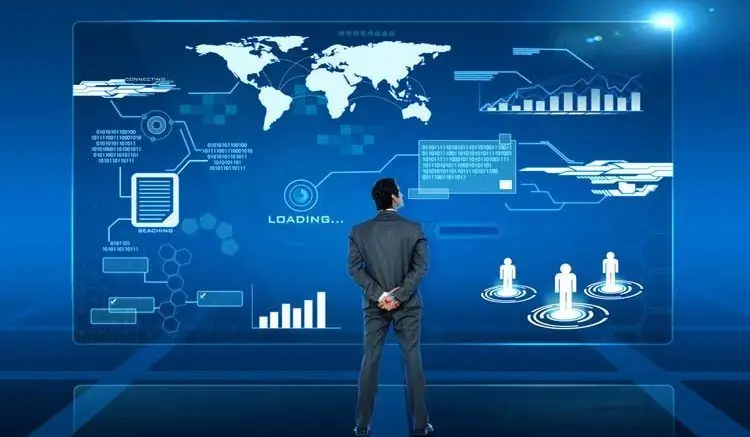
Es gibt keine renditestarken Anlagen ohne Risiko, daher werden sie von denen gewählt, die bereit sind, für schnelle Gewinne gewisse Verluste einzugehen. Und solche Anleger haben Zugang zu Instrumenten mit unterschiedlicher Rentabilität. Wenn Sie sich die Zeit nehmen, die Zuverlässigkeit zu analysieren und zu überprüfen, können Sie in wenigen Monaten eine erhebliche Kapitalerhöhung erzielen
Holzhobeln: Arten, Ausrüstung und Verfahrenstechnik
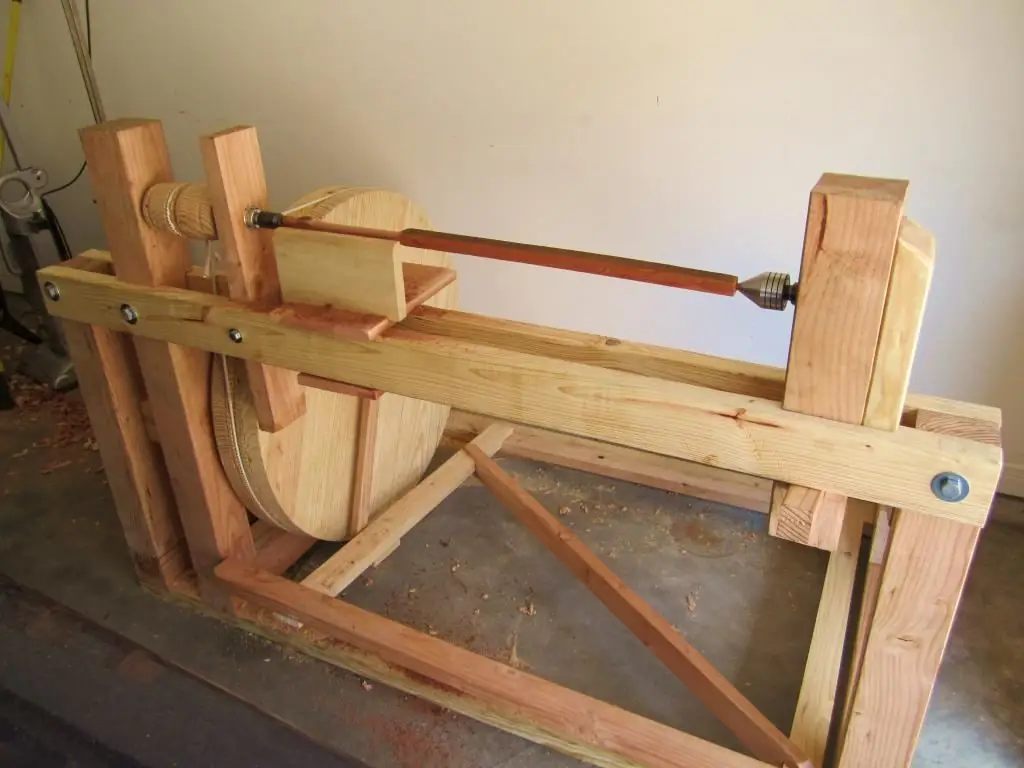
Holzhobeln ist eine der Verarbeitungsarten dieses Materials. Dieser Vorgang kann sowohl manuell als auch auf Maschinen durchgeführt werden. Es ist wichtig zu verstehen, dass jeder Holzrohling mit Hilfe des Hobelns die gewünschte Form und Gest alt annimmt
Stumpfschweißen: Geräte, Verfahren und Verfahrenstechnik
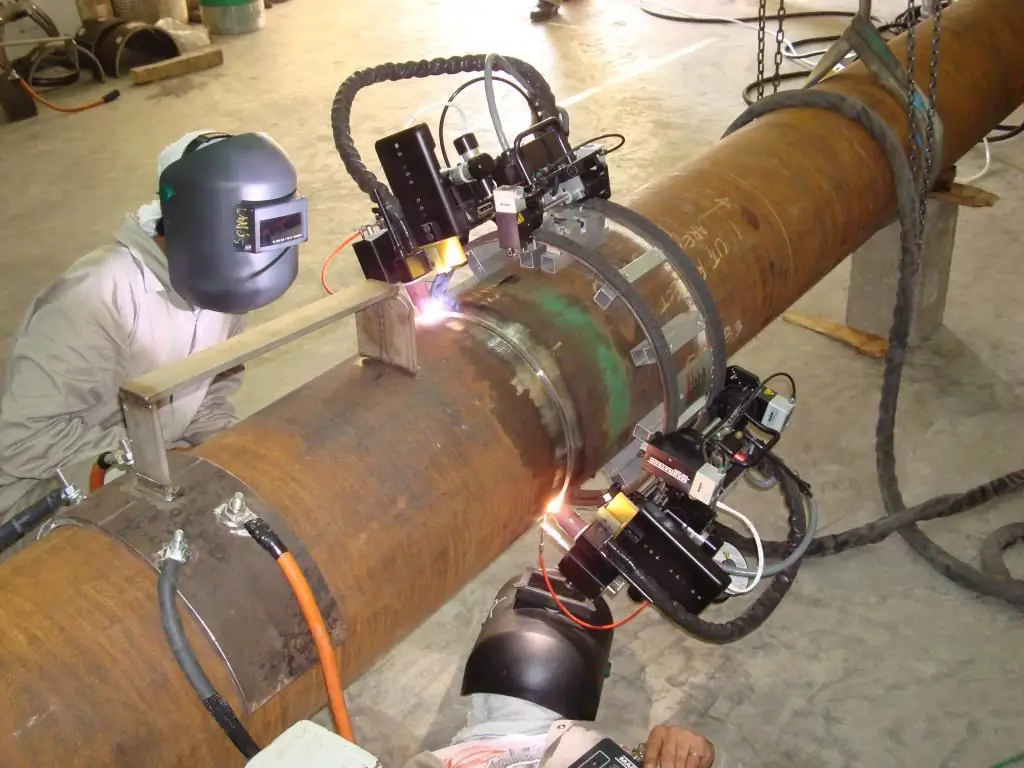
Merkmale des Abbrennstumpfschweißens. Arten von Stumpfschweißverbindungen sowie Ausrüstung, Verfahren und Technologie zur Durchführung des Stumpfschweißverfahrens. Schweißnahtfehler, die durch das Abbrennstumpfschweißen entstehen, sowie die Gründe für ihre Entstehung