2025 Autor: Howard Calhoun | [email protected]. Zuletzt bearbeitet: 2025-01-24 13:14
Die Verwendung von Einbettmodellen ist eine ziemlich beliebte Methode der Gießereiproduktion. Das Verfahren zeichnet sich durch die Komplexität des technologischen Prozesses und hohe Arbeitskosten für vorbereitende Prozesse aus. Daher wird es dort eingesetzt, wo es notwendig ist, die Abmessungen genau einzuh alten und eine hohe Qualität der Oberfläche der Teile sicherzustellen. So werden Turbinenschaufeln und Hochleistungswerkzeuge, Zahnersatz und Schmuck sowie komplex gest altete Skulpturen gegossen. Das Wesen des Wachsausschmelzverfahrens besteht darin, dass die Form zum Gießen einteilig ist, das Modell aus niedrigschmelzenden Materialien wird während des Gießens nicht entfernt, sondern geschmolzen. Dadurch wird eine sorgfältige Einh altung von Maßen und Entlastungen gewährleistet. In den vom Modell verbleibenden Hohlraum wird Metall gegossen. Nach Beendigung des Abkühlens wird die Form zerstört und das Produkt entnommen. Beim Gießen großer Serien werden die Produktkosten reduziert.
Vorteile der Methode
Der Hauptvorteil des Feingusses ist die Genauigkeit der Formübertragung und die geringe Oberflächenrauheit. Darüber hinaus stehen weitere Vorteile zur Verfügung:
- Produktion von leicht bearbeiteten Legierungsteilen verfügbar.
- Reduziert den Bedarf an weiterer Bearbeitung.
- Es werden Produkte gegossen, die sonst in Einzelteilen gefertigt und zusammengebaut werden müssten.
- Mit großen Serien wird eine Reduzierung der spezifischen Arbeitsintensität (pro Produkt) und seiner Kosten erreicht.
- Möglichkeit der Mechanisierung und teilweisen Automatisierung der vorbereitenden Operationen des Gießens selbst.
Diese Vorteile machen das Verfahren zu einem der beliebtesten und am häufigsten eingesetzten in der heutigen Metallurgie, insbesondere in Kombination mit modernen Folgegussverfahren.
Nachteile des Feingusses
Die unbestrittenen Vorteile der Methode, so scheint es, hätten ihre Dominanz unter anderen Methoden sicherstellen sollen. Trotz der Popularität des Feingussverfahrens haben jedoch Nachteile seine weitverbreitete Einführung verhindert. Der Hauptnachteil ist die Komplexität des mehrstufigen Prozesses. Es erfordert eine ziemlich komplexe und teure technologische Ausrüstung für die Vorbereitungsstufen. Für einfache Produkte, die in kleinen Chargen hergestellt werden, ist diese Methode mit höheren Kosten verbunden.
Für die wirtschaftliche Anwendung des Feingusses werden die Vor- und Nachteile des Verfahrens gegenübergestellt, die Entscheidung getroffenseine Wahl wird auf der Grundlage einer Bewertung des Preis-Leistungs-Verhältnisses getroffen. Daher wird es hauptsächlich für die kritischsten und teuersten Produkte verwendet, die auf andere Weise schwer zu erh alten sind, wie Turbinenschaufeln, Skulpturen, Hochgeschwindigkeitswerkzeuge usw. Ein weiteres Anwendungsgebiet sind Großgussteile, in wodurch durch den Skaleneffekt eine deutliche Kostensenkung erreicht werden kann.
Technologie
Die Feingusstechnologie ist ein mehrstufiger Herstellungsprozess, der relativ arbeitsintensiv ist. In der ersten Phase wird ein Urmodell hergestellt, das nach Durchlaufen aller Phasen des Endprodukts zum Standard für die Herstellung von Arbeitsmodellen wird. Für die Herstellung eines Meistermodells werden sowohl spezielle Modellaufbauten als auch traditionelle - Gips oder Holz - verwendet. Das Material des Meistermodells sollte Festigkeit und leichte Verarbeitbarkeit vereinen.
Ferner sieht die Feingusstechnologie die Erstellung einer Form vor, in die alle Arbeitsmodelle gegossen werden. Formen bestehen aus Gips, Gummi, Silikon, seltener aus Metall. Strukturell muss es notwendigerweise abnehmbar und für eine wiederholte Verwendung ausgelegt sein. Die Form wird mit einer Modellmasse gefüllt, nach dem Aushärten zerlegt und das nächste Arbeitsmodell entnommen.
Bei der Herstellung von Einzelstücken oder Kleinserien werden die Phasen der Erstellung eines Master-Layouts und einer Form übersprungen, und ein Layout (oder mehrere) wird durch manuelles Formen des Materials erstellt.
Der nächste Schritt im Feingussverfahren istFertigung rund um das Layout (oder Block von Layouts) der Gießform. Diese Matrizen sind strukturell bereits untrennbar und wegwerfbar, wodurch eine sorgfältige Einh altung der Abmessungen und Rauhigkeiten des Produkts erreicht werden kann. In der modernen Industrie werden zwei Arten von Formen verwendet - traditionelle Sand-Ton-Formen zum Gießen in den Boden und Schalenformen - für die Herstellung präziser und teurer Teile.
Nachdem die Form fertig ist, wird das Modell daraus durch Erhitzen oder Blasen mit überhitztem Dampf geschmolzen. Schalenformen werden zusätzlich durch Erhitzen auf 1000 ˚С verstärkt.
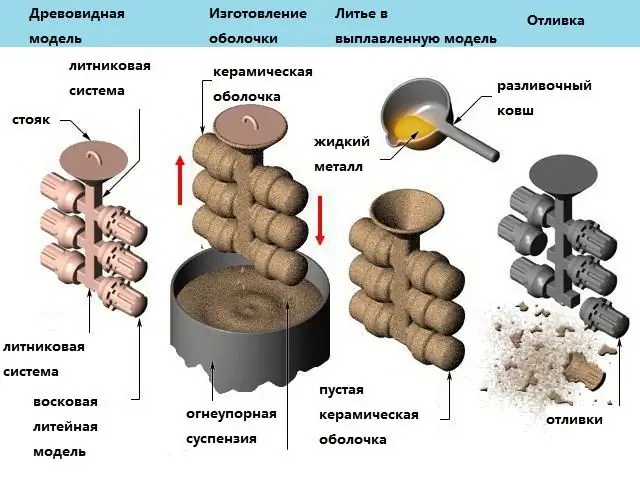
Die letzte Phase des Prozesses umfasst das eigentliche Gießen des Produkts, seine Abkühlung unter natürlichen Bedingungen oder durch ein spezielles Verfahren in einem Thermostat, die Zerstörung der Form und die Reinigung des Produkts. Das Verfahren ermöglicht es, hochwertige Gussteile mit einem Gewicht von mehreren Gramm bis zu mehreren zehn Kilogramm zu erh alten.
Modellreihen
Das Material zur Herstellung des Layouts muss bestimmte Eigenschaften aufweisen. Es sollte folgende Eigenschaften haben:
- Plastizität in der festen Phase. Es ist notwendig, die Form des zukünftigen Produkts genau zu wiederholen und gegebenenfalls zu korrigieren.
- Stärke. Das Modell muss dem Formungsprozess ohne Verformung standh alten.
- Schmelzbar. Das Rendern eines Modells sollte nicht viel Zeit und Energie erfordern.
- Geschmolzene Fließfähigkeit. Die Komposition sollte leicht in alle Aussparungen und Details des Reliefs eindringen und die Umrisse des zukünftigen Details genau wiederholen.
- Wirtschaft. Besonders wichtig für die Großserienfertigung.
Für Modellaufbauten wird meist eine Mischung aus Stearin und Paraffin verwendet. Diese Materialien ergänzen erfolgreich ihre Parameter und kompensieren den unzureichenden Schmelzpunkt von Paraffin und die übermäßige Viskosität von Stearin.
Zusammensetzungen auf Basis von Braunkohlewachs sind in der Industrie nicht weniger beliebt. Seine Haupteigenschaften sind Feuchtigkeitsbeständigkeit, Festigkeit und die Fähigkeit, sehr glatte Beschichtungen zu bilden, was besonders wertvoll für die Produktmodellierung ist.
Es werden auch Verbindungen verwendet, die aus einer Mischung von Braunkohlewachs, Paraffin und Stearin bestehen.
Formenbau
Für die Herstellung einzigartiger Produkte wird ein Layout erstellt, indem ein Stück Modellmaterial manuell oder nach Vorlage ausgeschnitten wird. Auch Modelle in Form von Rotationskörpern werden auf Drehbänken hergestellt. In letzter Zeit hat sich die Methode des 3D-Drucks von Modellen immer weiter verbreitet. Es eignet sich sowohl für Einzellayouts als auch für Kleinserien.
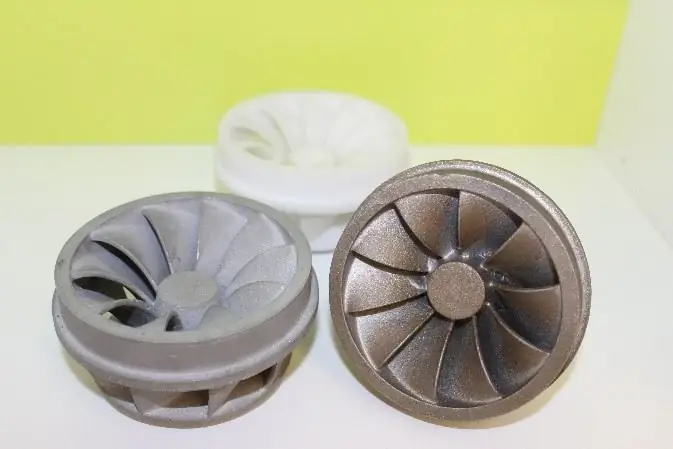
Die Kosten für einen modernen industriellen 3D-Drucker sind immer noch hoch, aber aufgrund der einfachen Umkonfiguration von einem Produkt zum anderen kann er bei einer großen Anzahl von heterogenen Kleinserienaufträgen zu einem effektiven Modellbauwerkzeug werden.
Um eine große Anzahl identischer Layouts zu erstellen, wird eine Matrize aus Gips, Gummi, Silikon oder Metall hergestellt. Arbeitslayouts entstehen wiederum durch Eingießen in eine Matrize. Die Form muss konstruktionsbedingt zusammenklappbar sein, um die Möglichkeit zu gewährleisten, eine bestimmte Anzahl von Modellen herzustellen. Auch das gewählte Material sollte eine solche Möglichkeit bieten, daher werden ihm solche Anforderungen wie Festigkeit, Dichte, geringe Rauhigkeit und chemische Inertheit gegenüber dem Layout auferlegt. Zudem muss die Formmasse möglichst wenig am Mock-up haften, damit sich die fertigen Mock-ups leicht entnehmen und die Maße einh alten lassen. Eine wichtige Eigenschaft der Form ist ihre Festigkeit und Verschleißfestigkeit, insbesondere bei großen Serien.
Modelle und Blöcke erstellen
Ein weit verbreitetes Verfahren zur Herstellung von Einbettmassemodellen ist das Gießen unter geringem Druck in Formen. Die Injektion des flüssigen Gemisches erfolgt sowohl manuell mit Kolbenspritzen als auch mit mechanischen, hydraulischen oder pneumatischen Kompressoren. Bei der Verwendung von Braunkohlewachs ist es aufgrund seiner hohen Viskosität erforderlich, die Rohrleitungen zum Zuführen der Zusammensetzung zu beheizen. Modelle aus expandiertem Polystyrol werden durch Extrusion auf automatisierten Formmaschinen hergestellt.
Zur Steigerung der Wirtschaftlichkeit und Reduzierung der Arbeitsintensität bei der Serienfertigung kleiner Gussteile werden deren Layouts zu Blöcken zusammengefasst. Über den Blöcken werden Angusssysteme gebildet, indem individuelle Layouts mit einem Handlötkolben auf die Gusskanäle aufgebracht werden. Bei Einzelgüssen oder Kleinserien werden die Modelle von Hand gefertigt.
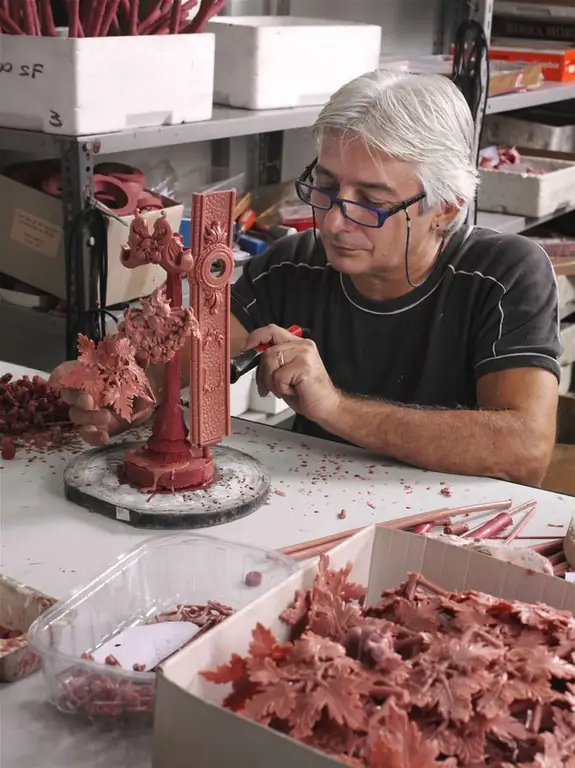
Bei der Bildung von Angusssystemen ist auf einen turbulenzfreien Fluss der Schmelze und eine gleichmäßige Füllung aller Elemente der Matrix zu achten. Beim Ausfüllen eines Formulars von PGS müssen Sie auch das gleichmäßige Ausfüllen aller überwachenÖffnungen zwischen Angüssen und verhindert Beschädigungen.
Form herstellen
Bei dem betrachteten Feingussverfahren gibt es zwei Haupttypen von Formen:
- Sand-Ton-Mischungen (SGM).
- Schale.
Flüssigwachsgussformen werden hauptsächlich bei der Herstellung von Kleinserien von Produkten verwendet, die keine sehr hohe Genauigkeit erfordern. Der Prozess ihrer Herstellung ist ziemlich arbeitsintensiv und erfordert hohe und oft einzigartige Fähigkeiten von Modellbauern und Formern. Eine Teilmechanisierung bietet sich nur für bestimmte Arbeitsgänge an, wie das Aufbereiten und Einfüllen des Formsandes, sein Stampfen.
Maskenformen hingegen werden zur Herstellung von Teilen verwendet, die eine besondere Fertigungspräzision erfordern. Der Prozess ihrer Herstellung ist komplexer und langwieriger, eignet sich aber besser für die Mechanisierung.
Bodenguss
Dies ist die früheste von der Menschheit beherrschte Methode der Metallverarbeitung. Es wurde von unseren Vorfahren gleichzeitig mit dem Beginn der Verwendung von Metallprodukten als Waffen, Werkzeuge oder Utensilien, also vor etwa 5.000 Jahren, gemeistert. Geschmolzenes Metall wird in eine vorbereitete Matrix aus einer Mischung aus Sand und Ton gegossen. Die frühesten Orte der Metallverarbeitung entstanden dort, wo sich in der Nähe Metallvorkommen in Form von Nuggets und Seifen befanden. Ein typisches Beispiel ist das Kasli-Werk im Ural, weltberühmt für seinen Eisenspitzenguss.
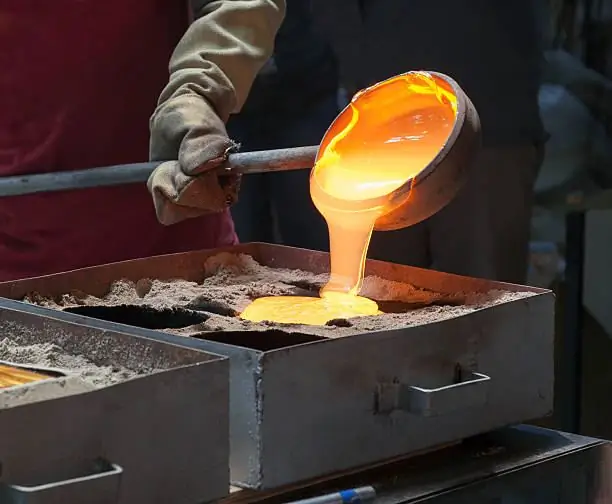
Das Feingussverfahren wird zur Herstellung von Metallprodukten verwendet - sowohl Eisen- als auchfarbig. Und nur bei Metallen, die in der flüssigen Phase eine erhöhte Reaktionsneigung aufweisen (z. B. Titan), müssen Matrizen aus anderen Zusammensetzungen hergestellt werden.
Der Produktionsprozess des Gießens in PGS besteht aus den folgenden Phasen:
- Modellbau;
- Kolben vorbereiten;
- Einfüllen und Verdichten der Mischung im Kolben;
- Metallguss;
- Guß entfernen und reinigen.
Formular von ASG - Einmalgebrauch. Um das fertige Produkt zu erh alten, muss es zerbrochen werden. Gleichzeitig steht der größte Teil der Mischung zur Wiederverwendung zur Verfügung.
Als Werkstoffe für ASG werden Zusammensetzungen aus überwiegend Quarzsanden unterschiedlicher Körnung und plastischen Tonen verwendet, deren Geh alt zwischen 3 und 45 Prozent liegt. So werden beispielsweise Kunstgüsse mit einer Mischung mit 10-20 % Tonanteil hergestellt, bei besonders großen Gussteilen wird der Tonanteil auf 25 % eingestellt.
Zwei Subtypen werden verwendet:
- Facing Mischungen. Sie befinden sich an der Innenfläche der Kokille und interagieren mit dem geschmolzenen Metall. Sie müssen hitzebeständig sein, dürfen nicht durch Temperaturunterschiede und die daraus resultierenden Spannungen zerstört werden. Diese Mischungen haben eine feine Körnung, um die Details der Oberfläche sorgfältig zu vermitteln. Die Fähigkeit des Gemisches, Gas zu passieren, ist ebenfalls sehr wichtig.
- Füllmischungen. Sie werden zum Hinterfüllen zwischen der Vorsatzschicht und den Wänden der Küvette verwendet. Sie müssen dem Gewicht des gegossenen Metalls standh alten, die Form des Produkts beibeh alten und zur rechtzeitigen und vollständigen Entfernung von Gasen beitragen. Hergestellt aus billigeren Sandsorten,wiederverwendbar.
Wenn die Gießgase nicht durch die Formsandmassen, sondern durch das Angusssystem entweichen, kommt es zu Gussfehlern, die zur Verheiratung führen.
Die traditionelle Technologie des Eingießens in den Boden wird im Film "Anrei Rublev" von A. Tarkovsky ausführlich dargestellt. In der Kurzgeschichte „Die Glocke“leitet der junge Mann Boriska, der Sohn eines verstorbenen Meisters, eine Gießerei und gießt eine Kirchenglocke.
Muschelguss
Das Feingussverfahren in Formschalen zeichnet sich durch beste Übertragung der Produktabmessungen und geringe Oberflächenrauhigkeit aus. Das Modell besteht aus schmelzbaren Verbindungen, wie z. B. Braunkohlewachs. Gießereien verwenden auch häufig die Zusammensetzung von Paraffin-Stearin in gleichen Anteilen. Bei großen Gussstücken werden Salze in das Modellmaterial eingearbeitet, um das Modell vor Verformung zu schützen. Durch Eintauchen in die Lösung wird das Modell in 6-10 Schichten mit einer Hochtemperatursuspension überzogen.
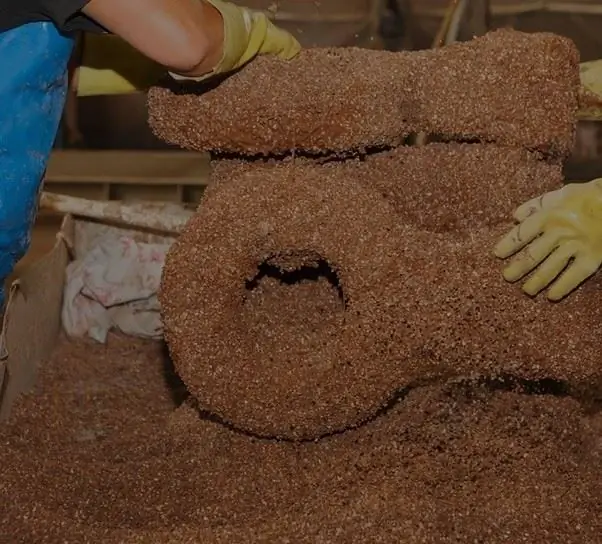
Als Bindemittel dienen hydrolysierte Silikate, als hitzebeständige Einstreuung werden Elektrokorund oder Quarzkristalle genommen. Formschalenwerkstoffe zeichnen sich durch hohe Festigkeit, geringe Hygroskopizität und hervorragende Gasdurchlässigkeit aus.
Die Anlage wird in einer Atmosphäre aus gasförmigem Ammoniak getrocknet. Im nächsten Schritt wird die Form auf 120 ˚C erhitzt, um das Paraffinmodell zu entfernen. Die Reste der Mischung werden mit überhitztem Wasserdampf unter hohem Druck entfernt. Als nächstes wird die Form bei Temperaturen bis zu 1000 ˚С kalziniert, was zu ihrer endgültigen Fixierung und Entfernung von Substanzen führt,die beim Gießvorgang als Gase freigesetzt werden können.
Die Granate wird in eine Art Kolben gelegt, der mit Stahlschrot bedeckt ist. Dies trägt dazu bei, die Konfiguration beim Füllen der Form mit Schmelze beizubeh alten und verbessert gleichzeitig die Bedingungen zum Abkühlen des Gussstücks. Die Schmelze wird in Formen gegossen, die auf 1000 ° C erhitzt sind. Nach dem Abkühlen des Produkts nach einem speziellen Programm in einem Thermostat wird die Form zerstört, das Gussteil entfernt und gereinigt.
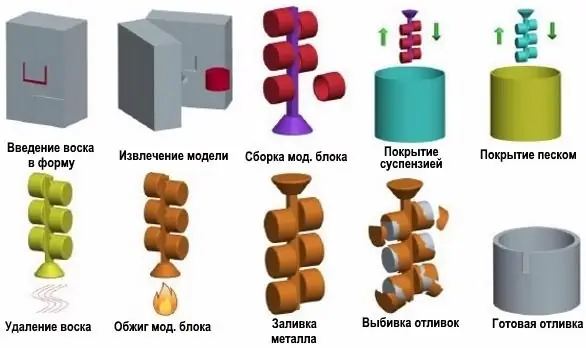
Der Hauptvorteil dieses Gießverfahrens ist die hohe Maßh altigkeit und geringe Oberflächenrauheit.
Weitere Vorteile der Methode:
- Gussteile aus schwer zerspanbaren Legierungen.
- Gussteile, die sonst Stück für Stück gegossen und dann wieder zusammengesetzt werden müssten.
Die Nachteile dieses Feingussverfahrens sind eine geringe Metallausnutzung und eine erhöhte Arbeitsintensität.
Präzisionsguss
Präzisionsfeinguss - so wird sowohl die Technologie als auch das Endprodukt selbst bezeichnet. Die hohe Gussgenauigkeit wird dadurch gewährleistet, dass bei der Vorbereitung der Form das Modell des Produkts nicht entnommen werden muss. Bei der traditionellen Methode ist die Herstellung einer Gussmatrize ein komplexer und sehr zeitaufwändiger mehrstufiger Prozess. Dies gilt insbesondere für komplex gest altete Gussteile mit Aussparungen, Vertiefungen und inneren Hohlräumen.
Zum Beispiel beim Gießen einer gusseisernen oder kupferfarbenen Vase mit variabler Oberflächenkrümmung muss man viele Tricks anwenden. Ja, zuerstDie untere Hälfte des Kolbens wird gefüllt, dann wird das Modell entfernt, umgedreht und die obere Hälfte gerammt. Das Modell muss zusammengesetzt werden, die Henkel der Vase bestehen aus zwei Elementen, sie werden in zwei Schritten durch den Modellhohlraum herausgezogen - zuerst das untere Element, dann das obere. All diese zahlreichen Drehungen und Schleifen können sich nicht positiv auf die Unversehrtheit der Formoberfläche und letztendlich auf die Genauigkeit der Beibeh altung der Abmessungen des Gussstücks und die Qualität seiner Oberfläche auswirken. Außerdem bleibt das Problem, die Teile der Kolben genau aufeinander abzustimmen und sicher aneinander zu befestigen.
Die Produktion von Feinguss weist diese Mängel nicht auf, erfordert keine so hochqualifizierten Modellbauer und reduziert die Arbeitsintensität der Vorgussvorgänge erheblich. Dies ist besonders ausgeprägt bei großen Gussserien.
Die Methode ermöglicht es, die 2-5. Genauigkeitsklasse nach GOST 26645-85 zu erreichen. Dadurch ist es möglich, hochpräzise Produkte wie Turbinenschaufeln, Schneidwerkzeuge, einschließlich Hochleistungsfräser und -bohrer, kritische hochbelastete H alterungen, kleine hochbelastete Fahrzeugteile, Werkzeugmaschinen und andere komplexe Mechanismen zu gießen.
Hohe Maßh altigkeit und hohe Oberflächengüte minimieren die Notwendigkeit einer weiteren Bearbeitung des Gussteils, was Metall spart und Produktionskosten senkt.
Ausrüstung
Die erforderliche Feingussausrüstung ist vielfältig und komplex. Unternehmen kombinieren sie zu einem einzigen und gut koordinierten Komplex,organisiert als Standort, Werkstatt oder separate Produktion.
Die Zusammensetzung des Komplexes hängt vom Produktionsumfang, der Größe, der Konfiguration und der Auflage der Gussteile ab.
Daher umfasst die Ausrüstung bei der Herstellung von Zahnersatz und Schmuck:
- Modelltabelle;
- Muffelofen mit Thermostat;
- ein Satz Skalpelle und Spatel zum Korrigieren der Form des Modells;
- Formtafel;
- Kolben;
- Behälter zur Lagerung und Aufbereitung von Formsand;
- Sandstampfer-Werkzeugsatz;
- Tiegel zum Schmelzen von Metall;
- Zange;
- Hammer, um die Form zu brechen.
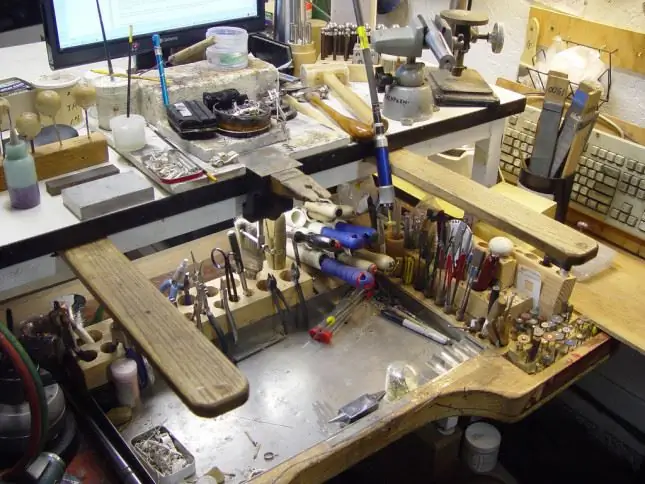
Dieser Produktionskomplex passt problemlos auf einen Tisch und in einen Schrank. Wenn beispielsweise Aluminiumgussteile in Serie hergestellt werden sollen, werden Geräte benötigt für:
- Formen und Gießen von Keramikformen;
- Trockenformen;
- Modellmaterial ausschmelzen und hitzebeständige Schicht auftragen;
- Gussteile von Formstoff reinigen.
Und schließlich die eigentliche Ausrüstung des Gießereikomplexes, die dazu bestimmt ist, eine Schmelze zu erh alten und sie in eine Form zu gießen. Es kann Casting-Ausrüstung sein:
- unter niedrigem Druck;
- zentrifugal;
- auf die übliche Weise der Schwerkraft.
Spritzguss- und Schleudergussmaschinen sind separate, hoch mechanisierte und automatisierte MaschinenProduktionskomplex, isoliert von der Atmosphäre des Ladens. Sie minimieren die manuelle Arbeit und die Exposition des Menschen gegenüber schädlichen Bedingungen. Abgedichtete Kammern, in denen sich die Komplexe befinden, sorgen für eine vollständige Erfassung und Reinigung von Abgasen, was die Umweltfreundlichkeit des Unternehmens erheblich erhöht.
Wachsausschmelzverfahren hat ein ziemlich hohes Entwicklungspotential, insbesondere in Kombination mit fortschrittlichen Formenbau- und Gießtechniken.
Empfohlen:
Welsumer Hühnerrasse: Beschreibung, Inh alt, Vor- und Nachteile, Bewertungen
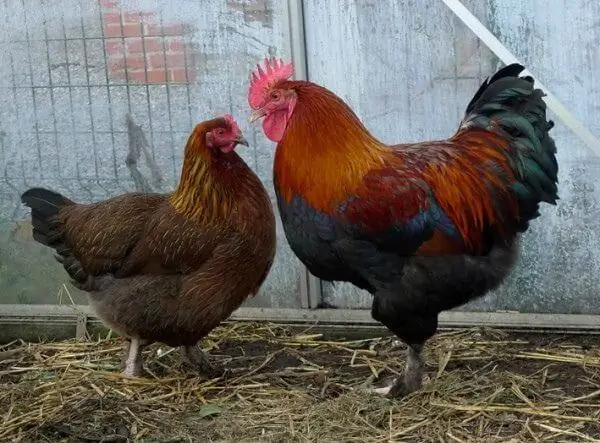
Für private Haush altsgrundstücke wird die Hühnerrasse nicht immer nach Produktivität ausgewählt, für einige ist das Aussehen wichtig. Es ist schön, wenn Vögel mit hellem Gefieder durch den Hof laufen, die keiner besonderen Pflege bedürfen. Noch besser, wenn äußere Schönheit mit hervorragender Leistung kombiniert wird. Diese Anforderungen werden von der Welzumer Hühnerrasse erfüllt. Sie hat viele positive Eigenschaften, weshalb sie oft in privaten Hinterhöfen angebaut wird
Investieren in Investmentfonds: Rentabilität, Vor- und Nachteile. Regeln für Investmentfonds
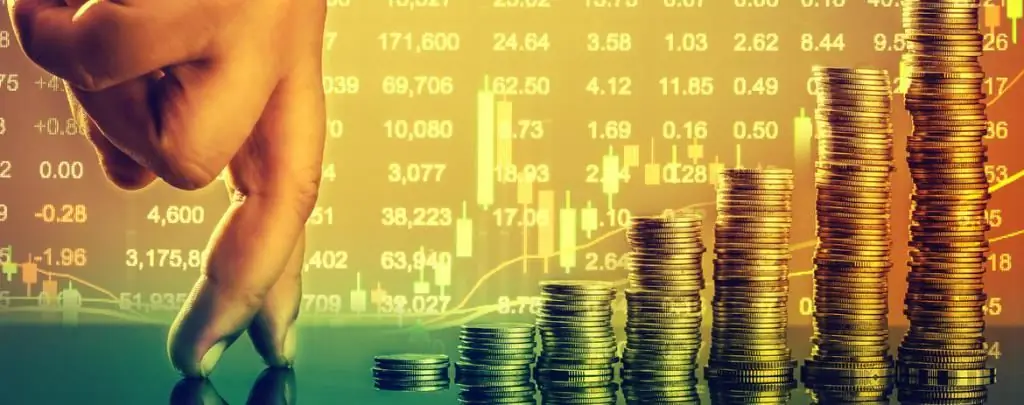
Ein so interessantes Finanzinstrument wie ein Investmentfonds (auch bekannt als Investmentfonds) ist vor relativ kurzer Zeit auf dem Gebiet der ehemaligen Sowjetunion erschienen. Und es sei darauf hingewiesen, dass sie in der allgemeinen Bevölkerung nicht sehr bekannt sind. Daher wird im Rahmen des Artikels nach der Antwort auf eine Frage gesucht: Was sind Investmentfonds?
Plexiglasgravur: Vor- und Nachteile, Technik, Ausstattung
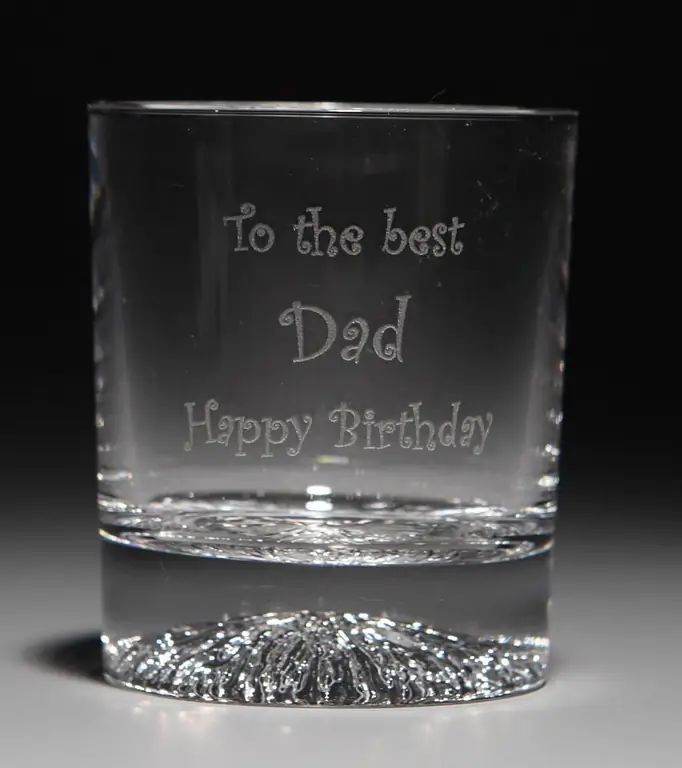
Plexiglasgravur gilt als malerisches Handwerk. Eine Souvenirfigur, Buntglasfenster oder ein Glastisch, die mit exquisiten Zeichnungen verziert sind, verkörpern einen feinen künstlerischen Geschmack. Beiz- und Sandstrahltechnologien gehören der Vergangenheit an. Heute kann jede Person mit Hilfe einer Lasermaschine ein sehr detailliertes Muster erstellen
Bodenbearbeitung vor der Saat: System, Technik, Verfahren, Ziele
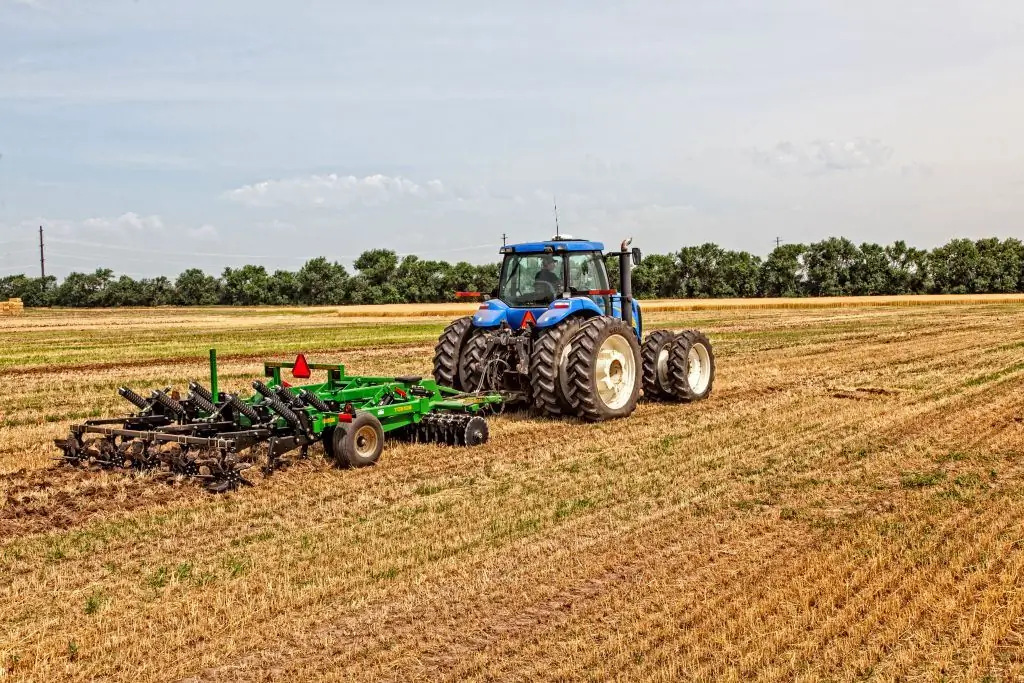
Wahrscheinlich hat jeder, der sich für Landwirtschaft interessiert, einen Begriff wie Vorsaatbearbeitung gehört. Dies ist eine wirklich wichtige Arbeit, von der viele Menschen, die sich nicht für dieses Thema interessieren, noch nicht einmal gehört haben. Und es ist völlig vergebens - durch eine korrekte und rechtzeitige Verarbeitung können Sie hervorragende Ergebnisse erzielen, sodass es für jeden nützlich ist, zumindest kurz etwas darüber zu erfahren
Kammertrocknung von Holz: Technik, Vor- und Nachteile
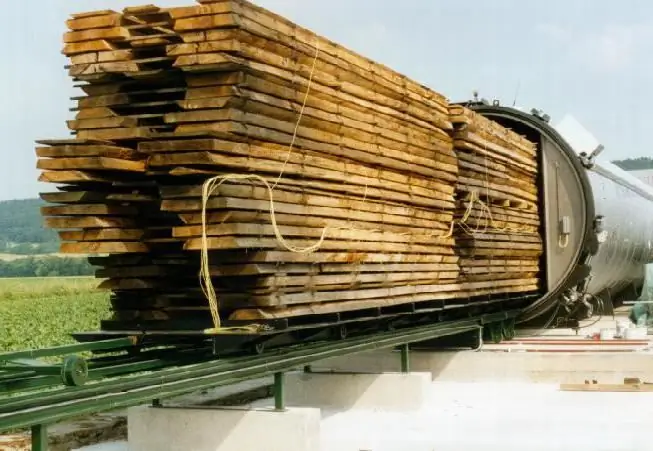
Der Artikel ist der Kammertrocknung von Holz gewidmet. Dabei werden die Trocknungstechnik, Stufen und Hauptoperationen sowie deren Vor- und Nachteile betrachtet